- Elkem
- Materials science & chemicals
- Materials science
- Rubber compounds
Polymer additives for rubber compounds
Polymer additives enhance the performance of rubber compounds, providing numerous useful features. These include better extrudability, flame retardancy, rheology, protection against dynamic fatigue, and more consistent fiber and halogen dispersion – across a wide range of applications.
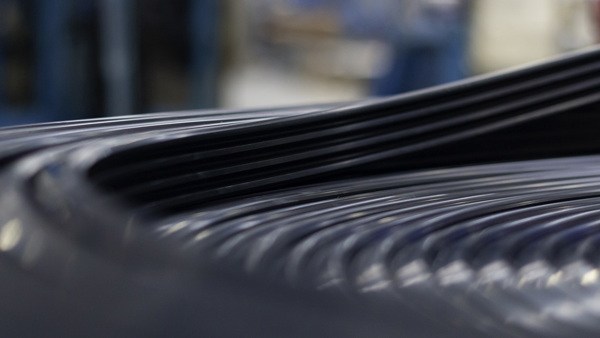
Improving rheology and processing: Smoother surfaces, reduced friction
Traditional process aids/lubricants are surface active substances that reduce the interfacial tension between surfaces, but this often leads to softening of the compound and reduction of physical properties, thermal ageing and oil/chemical resistance. Our alternative is 'the SIDISTAR™ way', using spherical particles, which reduce friction by minimizing the contact area between surfaces. When the particles are small enough, like the 150 nm particles of SIDISTAR™ product, only limited effects on properties can be expected.
SIDISTAR™ product for rubber compounds:
SIDISTAR™ R300
SIDISTAR™ R300 is a specially designed grey-coloured process modifier consisting of spherical, submicron particles of amorphous silicon dioxide.
Product data sheet
SIDISTAR™ R320
SIDISTAR™ R320 is a specially designed light-coloured process modifier consisting of spherical, submicron particles of amorphous silicon dioxide.
Product data sheet
SIDISTAR™ R320U
SIDISTAR™ R320U is a specially designed light-coloured process modifier consisting of spherical, submicron particles of amorphous silicon dioxide.
Product data sheet
SIDISTAR™ M220ST01
SIDISTAR™ M220ST01 is a specially designed light-coloured process modifier consisting of spherical, submicron particles of amorphous silicon dioxide.
Product data sheet
SIDISTAR™ XP320ST69
SIDISTAR™ XP320ST69 is a specially designed light-coloured process modifier consisting of surface modified spherical, submicron particles of amorphous silicon dioxide.
Product data sheet
SIDISTAR™ MB F21
SIDISTAR™ Master-Batch series are designed to provide you with easy dispersibility of Sidistar® in thermoplastics. Sidistar® MB F21 contains 50 % of SIDISTAR™ T120U in an ethylene acrylate carrier.
Product data sheet
Our product SIDISTAR™ offers improved processing and surface finish. These effects can be obtained both in rubbers as well as in thermoplastic compounds. Our customers use these properties in applications like cable compounds, flame retardant compounds, conveyor belts, as well as printer rolls.
The SIDISTAR™ 'ball bearing effect' has clear advantages for both cured and uncured compounds. Significant improvements in mixing energy and efficiency are seen, and there are cases where the number of mixing cycles could be reduced from three to two, at the same time as improving compound homogeneity.
Improving dynamic fatigue
By adding SIDISTAR™ additive to an elastomeric compound, you can achieve improvement of dynamic fatigue life up to 30–50%. These results can be obtained in a wide range of elastomers, such as NR, EPDM, BIIR and even FKM.
The fatigue improvement originates in the spherical shape and capability of dispersing down to primary particles. The primary particles in SIDISTAR™ have a mean size of 150 nm. The most commonly used SIDISTAR™ dosage, for these fatigue life improvements, lays in the range of 10–15 phr. There is little to no influence observed for physical properties and hardness of the final product.
Today, SIDISTAR™ is mainly used for its fatigue-enhancing properties in applications like anti-vibration pads, bushings and power transmission belts.
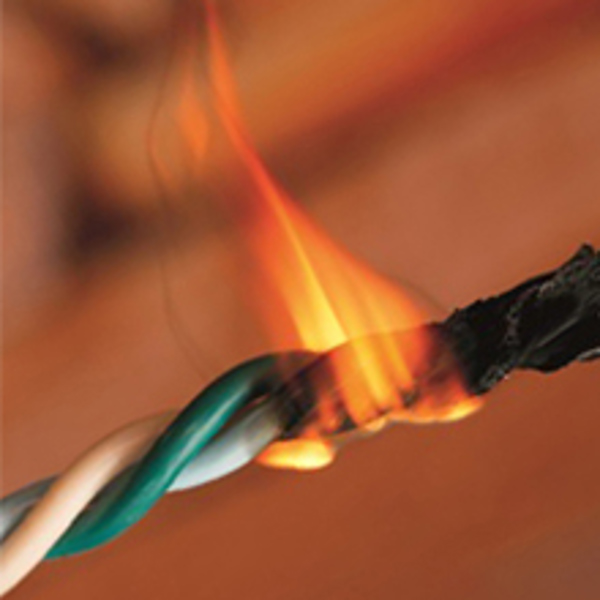
Improving flame retardancy
Whether you work with a flame-retardant system that relies on halogenated additives, or whether you prefer halogen-free systems, SIDISTAR™ additives can help you to find improved solutions.
Our product SIDISTAR™ acts as a synergist together with primary flame-retardant materials, to improve the morphology for improved char integrity.
Improving fiber dispersion for faster processing
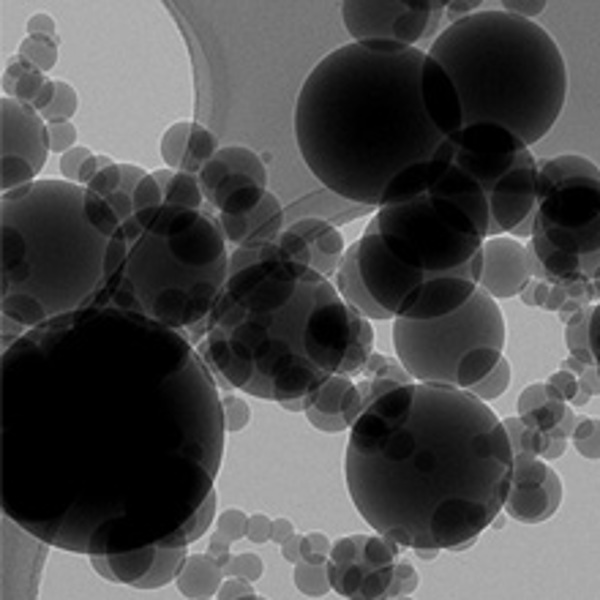
Incorporation of fibers into polymeric compounds can be a challenge, because they often remain floating on top of the compound and take a long time to incorporate and become fully 'wetted'.
By dry-blending fibres with SIDISTAR™, the incorporation is made a lot easier and at the same time the spherical particles result in a 'ball bearing' functionality, improving the processability of the final compound. This results in faster mixing, better anisotropic behavior, improved process ability, and improved product surface finish.
Improving special FKM compounds
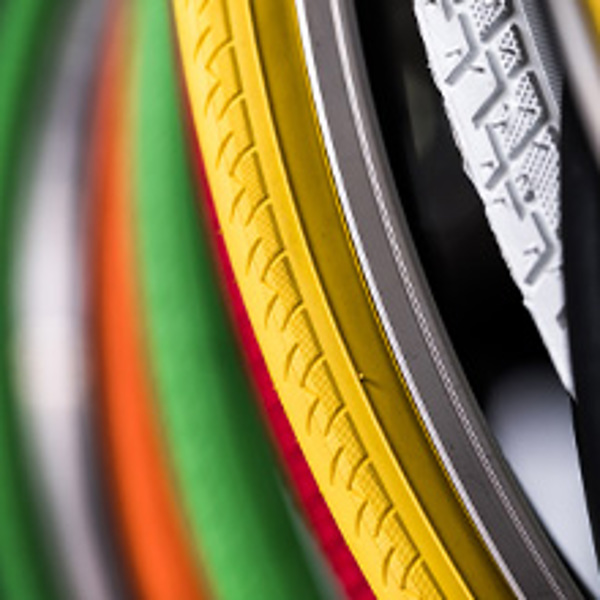
FKM elastomers are a special case in the rubber world. Unlike other rubber compounds, SIDISTAR™, with its very low specific surface of 20–30 m2/g, acts as a reinforcing filler for FKM elastomers.
SIDISTAR™ is capable of replacing N990 on a 1:1 basis. Physical properties will remain very similar, but dynamic fatigue properties will improve. Since SIDISTAR™ also has grades with an off-white colour, it allows production of coloured FKM compounds without compromising physical properties.
Polymer additives: Maintaining Elkem’s leadership through sustainable technology
Polymer additives and rubber product formulations are constantly evolving, driven by a need for greater energy efficiency, cost-effectiveness and sustainability requirements, including longer lifecycles and recyclability.
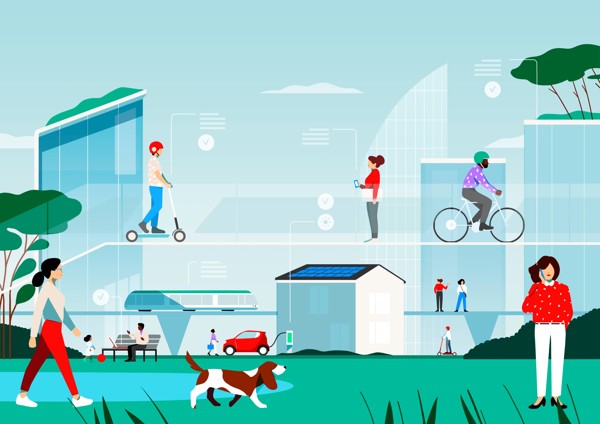
Sustainability at Elkem
To learn more about our sustainability initiatives, check our webpage.
More about polymer additives applications
Contact us
Take your business to the next level by partnering with a world-leading material manufacturer.