- Elkem
- Advanced manufacturing & industrial
- Pyrometallurgical Industry
- Cathode ramming paste
Cathode ramming paste
Avoiding metal leakage in aluminium electrolysis cells
Ramming paste is used to seal the cathode part of aluminium reduction cells, and so avoid metal leakage during operation. Since the 1980s, Elkem’s experts have been providing quality ramming paste to the aluminum smelting industry, and helping customers optimize its installation.
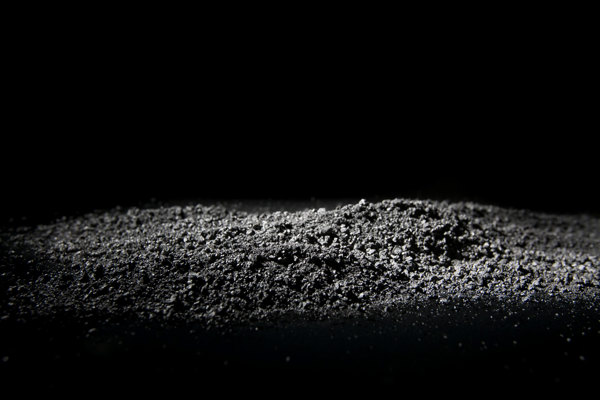
What is ramming paste?
Ramming paste is a granular material that is used to ensure a good seal within the cathodes of the electrolytic cells used for reduction of aluminium oxide to metallic aluminium using the Hall–Héroult process.
Ramming paste must be packed tightly, both around the peripheral seam of the cathode part of the pot and in the small joints between the cathode blocks themselves, and this is achieved with the aid of rolling or vibration equipment.
If this process is not carried out correctly, or if an inferior product is used, then shrinkage of the paste can result during baking, leading to leakage of molten aluminium and electrolyte. This can damage the cathode, and can cause disruption to cell operation or even premature pot failure.
However, such problems can be avoided by using a high-quality product, and by paying close attention to the packing process. If this is done, the paste should expand slightly when baked, providing a good seal for the entire lifetime of the electrolytic cell (typically 5–7 years).
High-quality ramming paste from Elkem
Since the 1980s, Elkem has been supplying high-quality ramming paste and technical expertise to the aluminium smelting industry. Today, we offer two products within our ELSEAL® ramming paste portfolio:
Product option
Description
ELSEAL® TE
Conventional product with low PAH emissions
ELSEAL® TCE
Conventional product with low PAH emissions and increased thermal conductivity
ELSEAL® G
Environmentally-friendly, odor-free product with zero PAH emissions
ELSEAL® GC
Environmentally-friendly, odor-free product with zero PAH emissions and increased thermal conductivity
Free-flowing
The amount of binder used in our ELSEAL® product is carefully optimized so that the product is dry enough to be free-flowing and therefore easy to handle. At the same time, we ensure that the formulation sinters effectively during the baking process, and therefore forms a long-lasting seal.
Low-emission, low-odor
Conventional ramming paste is formulated using coal-tar pitch as the binder. Although this form is highly effective, during handling and baking it releases harmful emissions, including small quantities of polycyclic aromatic hydrocarbons (PAHs). This requires the use of respiratory equipment by workers, as well as other environmental controls.
ELSEAL® G ramming paste overcomes this problem by using a water-borne mixture of organic compounds as the binder. This eliminates emissions of PAHs completely, and avoids any odor problems, making installation safer and more environmentally friendly. Type G paste has equivalent performance to our conventional Type TE product, and since its release in 2014 has had this performance proven in over 15,000 aluminium reduction cells.
Consistent quality
Our ELSEAL® ramming paste is produced to high specifications at our plants in Norway, Brazil and China. This ensures consistent product quality, for optimum performance every time.
Thermal conductivity options
Both types of ELSEAL® paste are available in two grades, providing a thermal conductivity of 7 W/(m·K) or 12 W/(m·K) after baking. We can provide advice on which is best suited to your electrolysis process.
Unparalleled application support
At Elkem, our offering to the aluminium smelting industry goes far beyond just supplying high-quality products to our customers – for more than 30 years, we’ve also been there to ensure that installation of the product proceeds seamlessly.
So if you buy ELSEAL® ramming paste from us, you’ll also benefit from:
- Installation guidance and auditing
- Problem-solving and technical advice
- Advice on temperature measurements during cell heat-up
- Collaboration on development work
- Regular on-site technical visits.
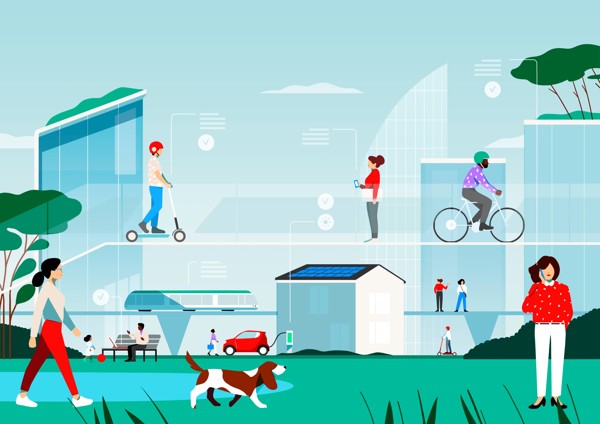
Sustainability at Elkem
To learn more about our sustainability initiatives, check our webpage.
Related products
Contact us
Reach out today to unlock your full potential with Elkem's safe, stable, and efficient solutions.