- Elkem
- Advanced manufacturing & industrial
- Refractories
- Microsilica for castables (monolithics)
Microsilica for castable refractory products
Improving high temperature and mechanical resistance for cast refractories
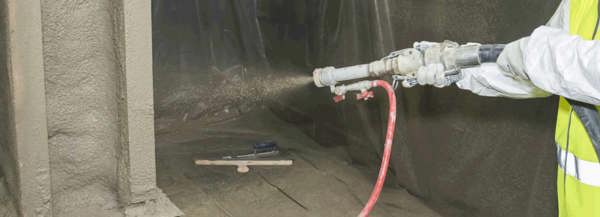
Refractories: Mastering a versatile and complex process
Castable refractories are either used as-delivered or after adding one (or several) liquids or additives. They must meet several, sometimes contradictory, specifications:
- Protecting the integrity of the kiln or furnace shell from elevated temperatures, while maintaining continuous high temperature and reducing heat loss when possible
- Preventing unwanted reactions, such as abrasion or chemical reactions, between the shell, the raw material and the end-product
- Resisting chemical attacks as well as mechanical stress due to extreme heat or periodical heating/cooling cycles.
Microsilica, which has become the generic term for silica fume, is a key ingredient in finding solutions in these complex processing challenges. It adds several beneficial properties to a refractory product thanks to its sub-micron particles, which contribute to efficient particle packing in concrete and refractory mixes, facilitate production of self-flowing castables with a minimum of water addition, and provide high temperature and mechanical resistance.
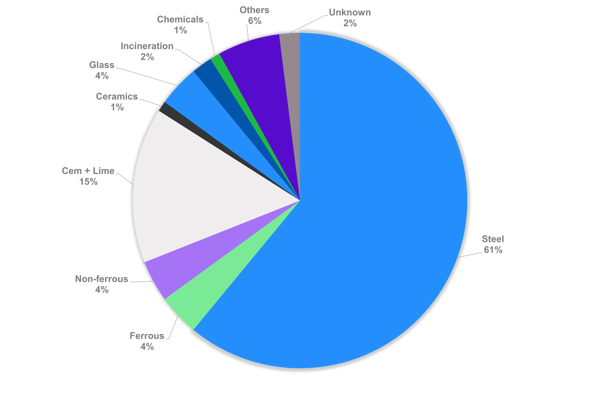
Making the right decision for castable refractory materials
Elkem Silicon Products is the global leader in microsilica technology since the 1980s, having been at the forefront in the development of refractory technology. Elkem MICROSILICA® powders, a co-product of silicon or ferrosilicon manufacturing mainly consist of ultrafine, amorphous spheres of silicon dioxide (SiO2). They feature high-purity properties, which can have a strong impact on the performance of refractory castables, particularly in the bonding phase of refractory at temperatures above 1250 °C.
Elkem MICROSILICA® also features control of particle size distribution (PSD), an important factor in developing dense refractory castables. It also provides the specific properties and benefits in all types of refractory materials, including low cement castables (LCC), ultra-low cement castables (ULCC) and no cement (NC) castables.
The benefits of Elkem MICROSILICA® refractory castable products include:
- Improved flow, particle packing and adjusted levels of densification, facilitating casting
- Reactivity during sintering, contributing to improved ceramic bonding at reduced firing temperatures
- Lower gas formation
- Versatility in application, including gunning mixes, shotcrete, etc.
- Gel bonding
- Improved hot-strength properties and guaranteed stability
Here is a non-exhaustive list of our product offering for castable refractory processing. Elkem experts, technicians and sales staff are available to explore the right solutions for your specific applications:
Refractory technology: Maintaining Elkem’s leadership through sustainable technology
Refractory technologies are constantly evolving, using alternative materials and product formulations, such as increasing development of raw materials and more enhanced and synthetic minerals. Changes are driven by a need for greater heat efficiency, cost-effectiveness and sustainability requirements, such as the use of recycled metals and less energy, a move to more low-carbon and renewable fuels, including the use of new technologies such as hydrogen and electric arc furnaces (EAFs) in metallurgy, etc. In R&D, Elkem refractory product design is also focusing on longer in-service life and greater safety for people and factories.
Discover the different silicon based materials for refractory applications, each with unique properties that are specifically crafted to meet the demands of high-temperature environments.
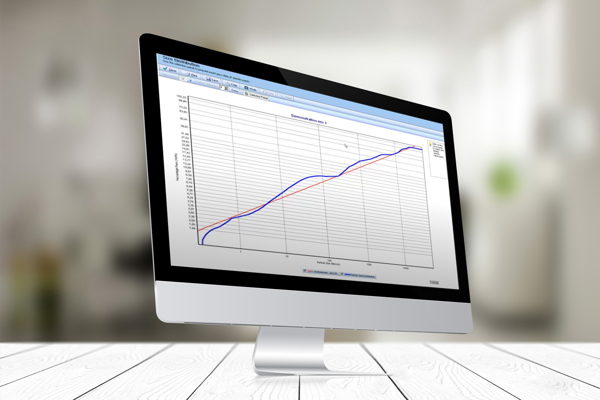
Elkem Materials Mixture Analyser
Get the best out of Elkem's silica fume (microsilica) by using our software to optimize your mixture
MORE ABOUT REFRACTORY APPLICATIONS
Contact us
Take your business to the next level by partnering with a world-leading material manufacturer.