- Elkem
- Energy & power
- Oil & gas
- Drilling fluids
Elkem oilfield applications for drilling & completion fluids
Addressing complex needs in drilling and completion, our high-caliber drilling fluid materials include weighting agents, water-based slurries and deflocculants for eliminating processing challenges.
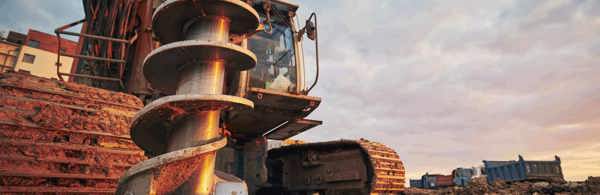
Elkem oilfield drilling and completion materials: solutions for all well sites
Oil companies and their service providers must deal with increasingly difficult drilling and completion challenges: access to and operation of more complex well sites (both onshore and offshore), greater productivity requirements and increased environmental and regulatory constraints.
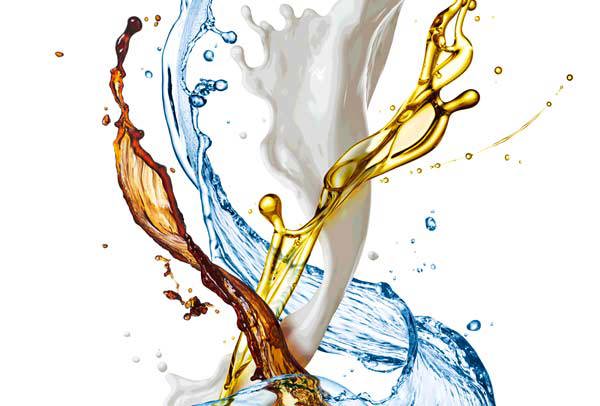
Elkem oilfield drilling fluid materials are value-added materials which are customer-focused and solution-driven, respecting all specifications, environmental regulations and the strictest quality assurance criteria.
Having served the oil & gas industry for over 60 years, Elkem was the first company to introduce micronized weighting materials, enabling the use of the same fluid for drilling and completion of the reservoir sections, thus streamlining production, symbolising its commitment to provide solutions with real added value.
Ensuring results in all drilling and completion operations
Elkem drilling and completion materials are specialty weighting agents which are designed and manufactured to eliminate customer processing challenges. They ensure the cementing of narrow pore to fracture pressure margin wells, provide very low rheological features for enhanced wellbore hydraulics, low sag potential and reduce overall cost for customers because of their hardness. They also reduce environmental impact because Elkem drilling fluids can be reused more often because their micronized weighting agents are acid-soluble, allowing for drilling and completion of the reservoir sections by using the same fluid in both operations.
Elkem’s main products include:
Weighting agents
MICROMAX®
MICROMAX® is a high performance weighting agent for drilling and cementing fluids. It is a manganese tetraoxide (Mn3O4) based material. MICROMAX® is not milled. MICROMAX® maintains a consistency in both PSD and almost perfect sphericity. It is both the size and shape which contributes to its unique properties. Unlike other weighting agents such as barite - which are milled and thus have angular morphology and wide PSD - MICROMAX® has spherical morphology and is produced in its finished form. MICROMAX® is 15 % denser and over 60 % harder than barite. However due to its sphericity and particle size, the abrasiveness and friction are significantly lower than barite. MICROMAX® can be used in a wide range of applications, including aqueous and non-aqueous drilling and completion fluids. MICROMAX® is PLONOR certified, and not classified as being dangerous to health. It is fully compatible with all common oilfield additives.
MICRODENSE®
To deal with the increase in drilling and completion of challenging wells, MICRODENSE® has been introduced to the global market. MICRODENSE® is a specially selected, high density, micronized ilmenite (iron titanium oxide, FeTiO), applicable for drilling, completion and cementing operations. MICRODENSE® has lower abrasiveness compared to commonly used weighting agents, and a magnetite content of less than 0.3 % by weight, preventing interference with logging tools. The usage of MICRODENSE® ensures improved fluids recovery at shakers and less dilution required to maintain properties as the high hardness of the Microdense particles prevents creation of fines in the fluid system. MICRODENSE® is partially acid soluble, making it suitable for drilling and completion of reservoir sections. By using the same fluid for drilling and completion operations, costly and time-consuming displacement can be avoided thereby reducing operational time.
By nature, MICRODENSE® has high hardness, preventing degradation and the resulting increasing surface area that can lead to poor ECD management. Lower dilution rates and less surface losses can be expected, all contributed to by the hardness of MICRODENSE®.
Water-based slurry
MAXFORM™
MAXFORM™ is a suspension of MICROMAX® in saturated potassium formate, producing a slurry of 19.2 ppg (2.30 SG). Higher density slurries are also available, and MAXFORM™ has been successfully tested to 22 ppg (2.62 SG) at 220°C. The MAXFORM™ slurry contains viscosifier, defoamer, dispersant, potassium formate brine, and MICROMAX®. It is buffered for stability. Potassium formate brine/MICROMAX® provides the base fluid to build a Maxform system. Normal use would require additions of fluid loss control chemicals, bridging material, etc, to produce a full system for drilling or completion applications.
MAXFORM™ can be used at the delivered density or diluted back with potassium formate brine. MAXFORM™ does not present harm to personnel compared to NAF’s and has a very good environmental profile thereby avoiding the disadvantages of using NAF’s. MAXFORM™ reduces formation damage compared to NAF’s. MAXFORM™ is very stable, easy to mix and maintain, and is a great substitute to NAF’s or expensive brines such as cesium formate.
Deflocculant
ESM D2
ESM D2 acts as a deflocculant in freshwater and brine-based drilling and completion fluids. ESM D2 works in both mono- and divalent brines, from sodium chloride to calcium bromide, or a mixture of potassium and cesium formates. It provides low, controllable rheologies, avoiding flocculation of weighing agents at elevated temperatures and densities that can lead to high fluid loss and sag. This product has been designed for MICROMAX® and MICRODENSE® weighting agents but works well with barite.
It provides stable drilling fluids at temperatures over 230 °C (446 °F) and at densities above 25 ppg (3.00 SG). ESM D2 is resistant to contaminants such as cement and salt, categorized by a green HSE profile being non-toxic and environmentally safe. General use of 5-20 kg/m³ (1.75 - 7 ppb).
Product safety information:
Drilling fluids
207 PSI Micromax®
213 SDS Maxform
1056 PSI ESM-D2TM
498 PSI Microdense®
Oilfield related pages
Contact us
Take your business to the next level by partnering with a world-leading material manufacturer.