- Elkem
- Energy & power
- Wind power
- Silicones reusable vacuum bag for infusion molding
Silicones Reusable Vacuum Bag for Infusion Molding
Reusable Vacuum Bag (RVB) silicone membranes improve the quality in composite molding
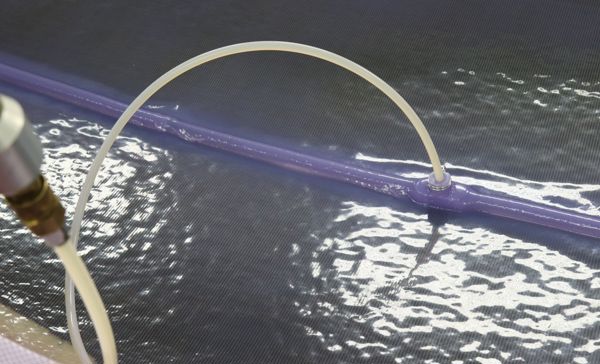
Silicone reusable vacuum bags (RVBs) for better composite infusion molding applications
Fiber reinforced polymer (FRP) composites are increasingly being used to make molded parts for a wide variety of industries: automotive (including trucks and off-road vehicles), renewable energy (components such as wind-power propellers), aerospace, marine construction, architectural structures, etc. These composites combine excellent mechanical properties with a low density, and feature high resistance to water, chemical and environmental pressure.
Traditionally, these materials were composed by a fiber like glass, carbon, aramid fibers as well as natural fibers or hybrid materials and other specialty combinations, and by resins like epoxies, unsaturated polyesters, DCPD polyesters, vinyl esters, phenolics, polyurethane and hybrids.
One of the methods to produce FRP composites and hybrid materials is the infusion molding process with the use of disposable plastic bag sheets that are manually placed and assembled by highly skilled operators. This process is extremely time consuming and generates a great deal of waste since every mold requires a change of bagging. In recent years, manufacturers focused their attention on reusable vacuum bag (RVB) membranes that increase productivity, reduce costs (in particular for larger batches) and improve the quality and consistency of parts produced. This process also contributes to better industrial safety and workplace cleanliness, while reducing the use of consumables and thus lowering waste.

Composite Molding with silicone reusable vacuum bag
Get an overview of the technical, industrial and economic challenges and advantages of composite molding using Reusable Vacuum Bags (RVBs), an innovative technology that improves the quality of critical parts, while lowering production costs in serial manufacturing.
However, because introducing RVBs into a production process can require capital investments and process changes, it is essential to choose the right technologies and products from the start. Depending on these choices and the composites being processed, RVBs can be reused from 20 to 300 times.
Elkem Silicones has been working with composite molding specialists for many years to constantly improve resin resistance to make bags last longer. This also applies to other molding technologies. Elkem Silicones has also developed the expertise to advise manufacturing companies in their industrial processes and provide them with the products they need for their specific molding applications and in particular RVBs. Feedback from the markets has been very positive, with many customers asserting that our bags last longer than those of the competition. Elkem Silicones specialists are available worldwide to work on these questions and other enhancements in producing RVBs and other processes for high-quality infusion composite molds.
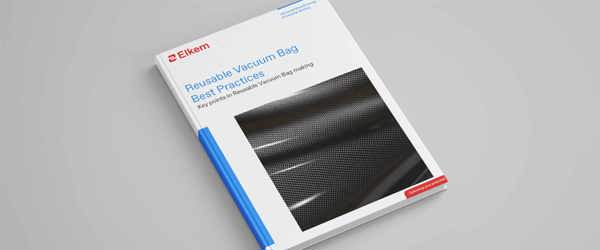
Reusable Vacuum Bag best practices
Discover best practices when implementing the reusable vacuum bag process to standardize your molding processes, increase your overall productivity, reduce the number of man-hours required for your molding operations...
Composites are also made using other molding processes (open or closed, using wet resin or prepreg fiber sheets) such as compression molding, injection molding, cast resins and several more. The use of Silicone Rubbers in these various processes is increasing, and this is due to the properties of release and chemical resistance of Silicones and to the flexibility of use of RTV Silicone rubbers, which can easily be adapted to the type of processing method.
Elkem Silicones has developed a range of RTV Silicones suitable for composites molding, which offer many advantages, including curing at room temperature, a definite plus compared to natural rubber or other synthetic materials.
Our products used in composites include:
-
BLUESIL™ RTV 3720 A&B and BLUESIL™ RTV 3720 A&B SC​ (Slow curing version), specifically developed to produce silicone RVBs for composite molds using vacuum resin infusion technology.
- BLUESIL™ RTV 3722 A&B, is developed to quickly produce a colorless elastomer of very high mechanical properties, that can be used to obtain silicone molds with excellent mechanical resistance.
- BLUESIL™ RTV 3723 A&B, is developed to produce a silicone bag on molds used for the processing of composites applying the "vacuum resin infusion" technology, and it is specifically designed to have an improved resistance to polyesters resins.
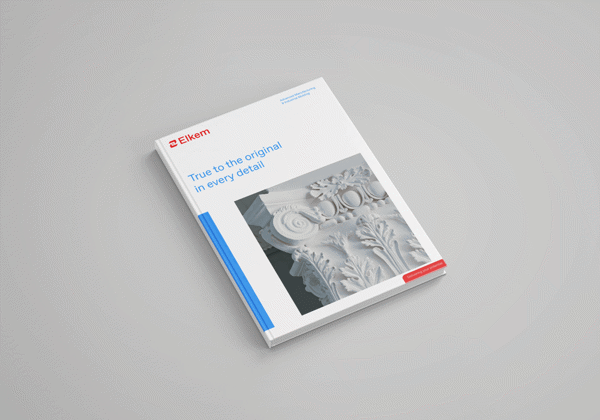
Silicone solutions for advanced molding & printing
For Elkem, innovation is the basis for the development of new products and services. We want to offer a competitive advantage to our partners and customers through...
Related application
Contact us
Take your business to the next level by partnering with a world-leading material manufacturer.