Silicone products for baby and childcare products
Silicones improve the quality and safety of childcare products
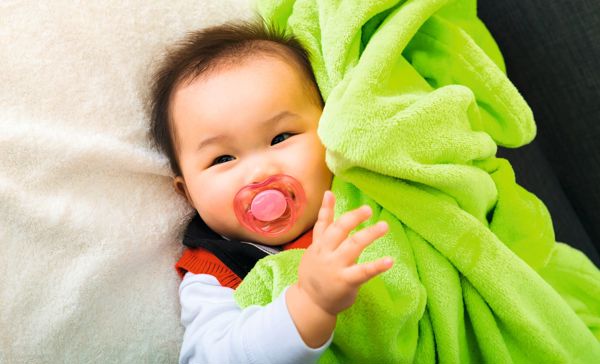
Children’s health, in particular during their infancy, is one of the greatest priorities of human beings throughout the world. Infants’ first contact with food, after breastfeeding, is through baby bottles. Traditionally, these baby bottles were made with glass which, while being hygienically very efficient, are heavy and, of course, brittle and prone to be broken. For a time, they were partly replaced with plastics, but these were not as hygienic because they were less heat-resistant and more difficult to sterilize and, as research advanced, were often found to contain unsafe or even toxic products. This safety problem was even more critical for bottle teats or nipples which were in direct contact with the baby’s mouth and ingested when sucked, and often contained what ultimately proved to be hazardous chemicals. Latex nipples, for their part, were opaque, making it difficult for parents to visualize the flow of baby formula during feeding time.
These limitations, inherent in glass, plastic and latex materials, as well as stricter regulatory obligations, led silicone rubber manufacturers to research, design and develop safe and convenient formulations for baby care products that comply with the most stringent medical and quality standards for food contact products.
Why choose silicone-based baby care products such as baby bottles?
- Silicone-based baby care products are safe for infants because they are biologically inert and biocompatible, containing no toxic substances such as Bisphenol A (BPA) or BPA substitutes (such as BPS used in plastics)
- Silicone baby bottles and nipples are heat resistant, making it easy to clean and sterilize
- They silicone-based products are odorless and to not retain the tastes of food, even after multiple uses
Why is silicone an efficient and cost-effective material to make quality baby care products for manufacturers?
Silicone rubber formulations can be adapted to meet specific mechanical properties that manufacturers require for making a wide range of bottles and nipples for different products targeting different age groups and the great diversity of demand in markets and territories worldwide. They offer excellent processability, which means they can be integrated into existing manufacturing systems or new facilities. Continuing research and development and growing production volumes are bringing the cost of raw materials and formulations down, with interesting price points for mass market manufacturers.
Here is a summary of the technical advantages of silicones for baby care products:
- Consistent purity and quality thanks to the Elkem mastery of the entire value chain, from silicon raw materials to finished silicone products
- Low viscosity and fast curing speed, increasing productivity
- Unique processing and formulations to ensure transparency of the finished product
- Excellent tear and tensile strength for safety and that enable complex designs
Our product offering
- LSR 8600 is a general-purpose Liquid Silicone Rubber (LSR) for food contact. It is highly adaptable to a wide range of processes, including injection and is therefore suitable for producing parts of various sizes and complex geometric designs.
- LSR 8800 is a non-post curing LSR. This means that, after injection molding (pre-curing), there has no need to put the part into an oven for post curing (200 ℃ for 4 hours). The injected parts can still achieve a stable Volatile Organic Compound (VOC) variation of less than 0.5 % according to EN 14350-2. This helps the manufacturer to improve production efficiency and offers a higher probability of passing the VOC test by avoiding possible uneven or incomplete post curing.
Finally, Elkem food contact silicone rubber products are ISO 10993 certified for biocompatibility and may meet chemical and physical property requirements as described in different national regulations.
Why choose Elkem for your baby care materials?
Our teams of silicone rubber experts have been serving the food processing and packaging industries for decades and have developed vast expertise for professional and domestic kitchenware and food consumption utensils. They are available to develop specific and innovative solutions to produce the formulations you need to optimize your manufacturing processes and provide your customers with the most versatile and safest food compatible rubber silicones.
They work with our Mix & Fix™ Centers, conveniently located near major food processing and utensil production centers on all continents.
Other services also include regulatory support, assistance to roll out productivity programs, training for teams and collaborative work on new developments.
Related products
Contact us
Take your business to the next level by partnering with a world-leading material manufacturer.