- Elkem
- Personal care & consumer goods
- Everyday goods
- Printers and photocopiers
Silicones for rollers and moving parts in printers and copiers
Silicone materials improve the performance of rollers and moving parts in office printers and copiers
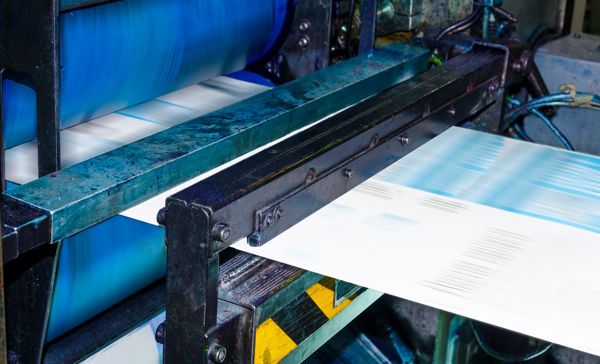
Photocopiers and printers are the core office automation devices for reproducing documents. They must ensure quick start in operations, provide speed in execution and produce accurate and visually compelling documents. They must also be cost-effective, offering low-energy consumption and minimal environmental impact. To achieve all these goals, printers and copiers need to have efficient rollers with a good compression set, efficient thermal and electrical conductivity to ensure that performance is always optimal and that moving parts do not deteriorate through thousands of repetitive cycles and long periods of use. Quality High-Consistency Rubber (HCR) silicone can enhance the performance of rollers and effectively extend the lifecycle of printers and copiers.
What are the main applications of silicone-based formulations in making office equipment rollers?
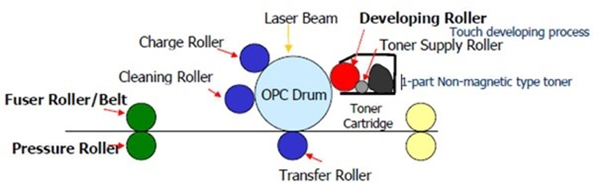
The main rollers involved in moving the paper through the printer or copier and which can benefit from the use of silicone materials are:
- The fuser roller and belt
- The pressure roller
- The developing roller
The Critical to Quality (CTQ) factors that manufacturers need to take into account for these parts are:
- Hardness (Nip width)
- Compression set (Durability)
- Rebound (Shape recovery)
- Heat resistance and high/low thermal conductivity
- Electrical conductivity
Why is silicone an efficient and cost-effective material to make quality printer and copier rollers for manufacturers?
Elkem formulations Liquid Silicone Rubber (LSR) and HCR can be formulated to exact specifications to provide the required features for each moving component. For example, in fuser rollers and belts, they can reduce thickness of the parts and enhance picture quality through an appropriate nip width for soft toner. In pressure rollers, they can enable a shift from hard rubber to sponges, leading to energy savings by limiting the escape of required heat levels.
Generally speaking, silicone rubber formulations can be adapted to produce specific mechanical properties for a wide range of rollers and moving parts. Silicone rubber is easy to process and cure, which means they can be integrated into existing manufacturing systems or new facilities. Continuing research and development and growing production volumes are bringing the cost of raw materials and formulations down, with interesting price points for mass market manufacturers.
Here is a summary of the technical advantages of silicones for copier and printer rollers:
- A wide range of viscosity, plasticity, elongation and hardness properties
- Excellent compression set
- Tensile strength
- Fast curing speed, increasing productivity
- Thermal and electrical conductivity control
Our product offering
- LSR 6800 is product series that has been specifically designed for rollers used in printers and copiers, for their versatility, processability and excellent characteristics, including compression set, thermal and mechanical properties, etc.
Why choose Elkem for making printer and copier rollers?
Our teams of silicone rubber experts have been serving a wide range office and industrial automation industries for decades and have developed vast expertise for process and product improvement. They are available to develop specific and innovative solutions to produce the formulations you need to optimize your manufacturing processes and provide your customers with the most versatile rubber silicones to serve their own customers.
They work with our Mix & Fix™ Centers, conveniently located near major office equipment production centers on all continents.
Other services also include regulatory support, assistance to roll out productivity programs, training for teams and collaborative work on new developments.
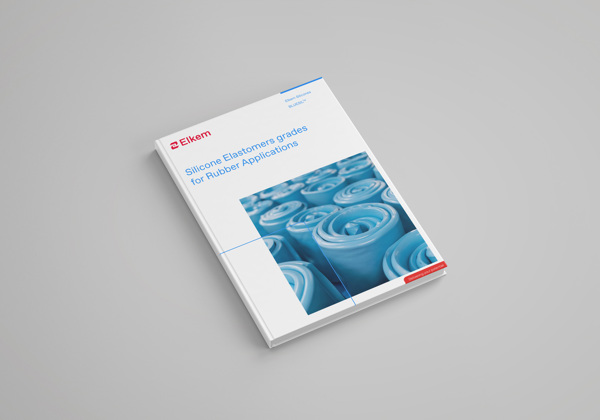
Related products
Contact us
Take your business to the next level by partnering with a world-leading material manufacturer.