- Elkem
- Materials science & chemicals
- Materials science
- Thermoplastics
Polymer additives for thermoplastics
Polymer additives enhance the performance of thermoplastics, providing numerous useful features. These include better extrudability, flame retardancy, rheology, protection against dynamic fatigue, and more consistent fiber and halogen dispersion – across a wide range of applications.
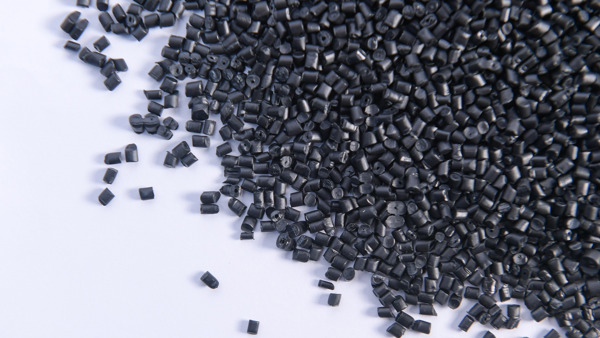
SIDISTAR™ product has interesting properties in thermoplastic compounds. Due to its morphology, it allows improvement of flame retardancy and improved processing. SIDISTAR™ product finds its way in multiple end use applications e.g; cable jackets, roofing membranes, and washdryer condensers because of its flame retardant synergy properties. But also in wood-plastic composites and foamed products and yarn spinning because of its process improving properties.
SIDISTAR™ product in thermoplastics
SIDISTAR™ T100
SIDISTAR™ T100 is a specially designed grey-coloured process modifier consisting of spherical, sub-micron, particles of silicon dioxide.
Product data sheet
SIDISTAR™ T120
SIDISTAR™ T120 is a specially designed light-coloured process modifier consisting of spherical, submicron particles of amorphous silicon dioxide.
Product data sheet
SIDISTAR™ T120U
SIDISTAR™ T120U is a specially designed light-coloured process modifier consisting of spherical, submicron particles of amorphous silicon dioxide.
Product data sheet
SIDISTAR™ M220ST01
SIDISTAR™ M220ST01 is a specially designed light-coloured process modifier consisting of spherical, submicron particles of amorphous silicon dioxide.
Product data sheet
SIDISTAR™ MB F21
SIDISTAR™ Master-Batch series are designed to provide you with easy dispersibility of Sidistar® in thermoplastics.
PDS SIDISTAR MB F21.pdf
Nucleating effect
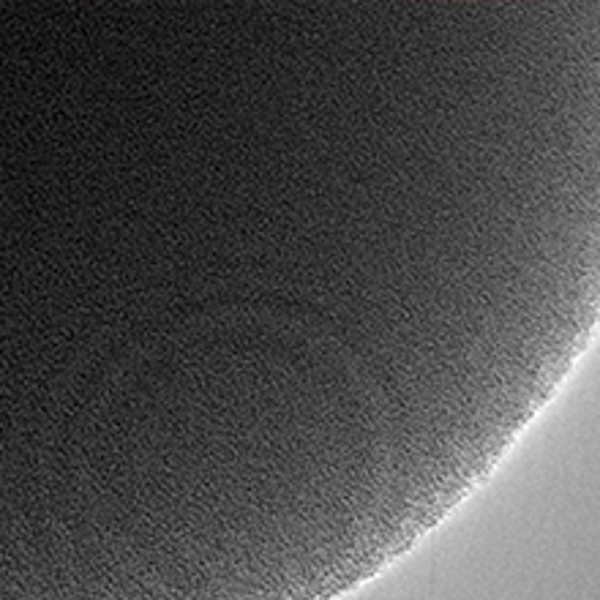
Due to the fact that our product SIDISTAR™ can be dispersed down to primary particles the material has a nucleating effect. It allows to produce a more uniform foam (closed cells), with smaller “bubbles”, this gives better strength as well as a greatly improved surface. E.g. a rigid, chemically foamed PVC, will become more uniform even when adding quite moderate amounts of SIDISTAR™ product. As the foam flows out of the extruder and the PVC is cooled, all gas filled cells will shrink, creating tiny dimples at the surface. SIDISTAR™ as a nucleating agent, will ensure that the foaming takes place in more places at the same time. By creating smaller cells with a more homogenous size throughout the material one obtain a reduction of the specified gravity of the final product.
Improving flame retardancy
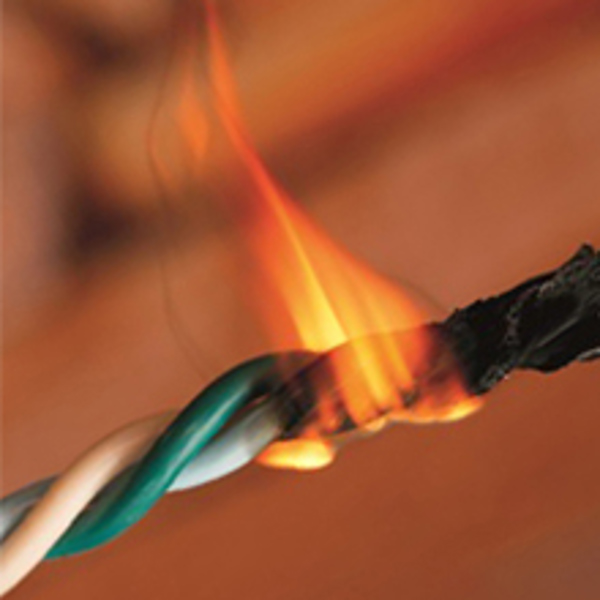
SIDISTAR™ product is a flame-retardant synergist which improves the char, by making it stronger and tighter. Our product SIDISTAR™ can reduce smoke development and burning droplets in e.g. UL94 tests. It has proven to be a strong synergist in combination with other flame retardants like: ATO, ATH, MDH, APP, phosphates and phosphinates, improving their efficiency. Compared to other Nano sized materials, our product SIDISTAR™ can easily be dispersed by standard equipment such as twin-screw extruders or other kneaders down to primary particles.
Improving rheology and processing
The tiny perfect spheres of SIDISTAR™ allow it to work as 'ball bearings' in a filled compound. As shear forces are applied, SIDISTAR™ particles minimize the contact area of solid particles and, as the spheres are not attached to the matrix, they are able to roll on contact.
This phenomenon results in a lower extrusion back-pressure, and a lowering of the mixing energy. SIDISTAR™ is often used, in low loadings, to reduce the build-up of 'die-drool' or 'plate-out'. Since the SIDISTAR™ spheres reduce the friction between the extrudate and the die, the extrudate will have a more uniform flow between core and mantel areas, ensuring that it passes more quickly across the contact area. As a result, the material does not 'stagnate' and the risk of overheating is reduced. With reduced 'plate-out', you get less downtime and waste, as well as a finer/smoother product surface.
Polymer additives: Maintaining Elkem’s leadership through sustainable technology
Polymer additives for thermoplastics are constantly evolving, driven by a need for greater efficiency, cost-effectiveness and sustainability requirements, including longer lifecycles and recyclability.
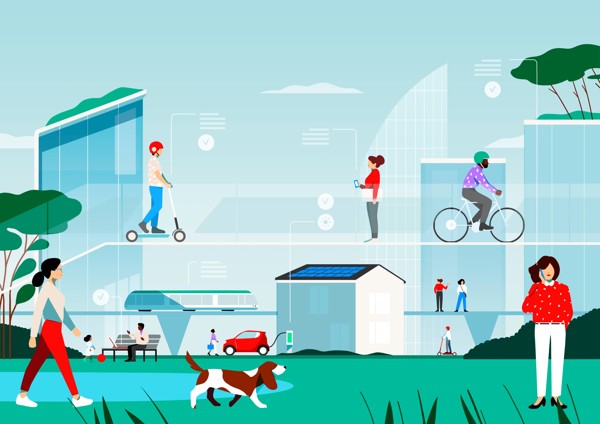
Sustainability at Elkem
To learn more about our sustainability initiatives, check our webpage.
More about polymer additives applications
Contact us
Take your business to the next level by partnering with a world-leading material manufacturer.