- Elkem
- Products
- Foundry alloys
- Our technical advice for your processes
- Surface defects
Surface defects
Our advice can help you eliminate surface defects and hydrogen pinholes
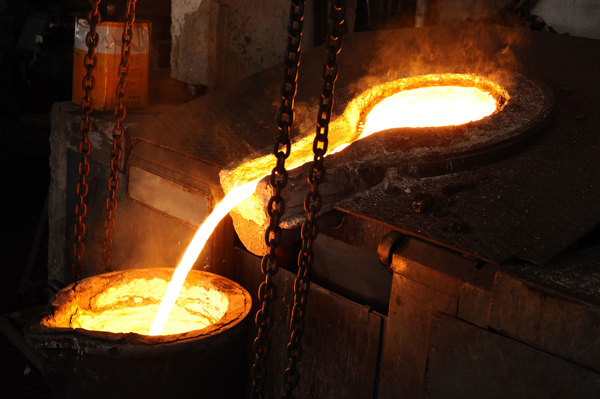
Hydrogen pinholes
Many surface defects in cast iron such as hydrogen pinholes can easily be avoided. Titanium, aluminium and moisture are the common causes of hydrogen pinholes in greensand systems. Both Al and Ti lower the surface tension of the liquid iron allowing gasses to be more easily picked up.
Hydrogen pinholes have a distinctive graphite lining within the cavities. Elkem produces a range of MgFeSi alloys and inoculants with very low Al to help keep the aluminium content below the critical levels for pinhole generation.
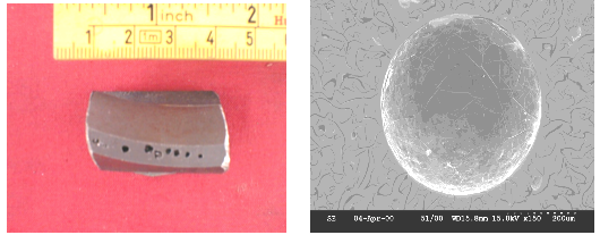
Hydrogen can also be a problem in ductile iron where it tends to form porosities.
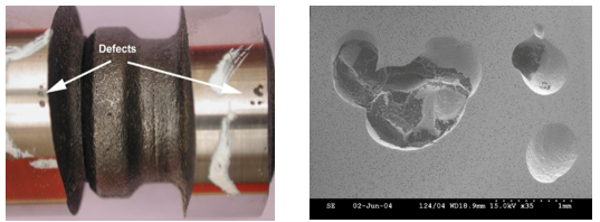
Hydrogen pinholing can also be caused by the following reactions, leading to a nodule-depleted zone:
H2O + C —> H2 + CO. Followed by: 2 CO —> C + CO2.
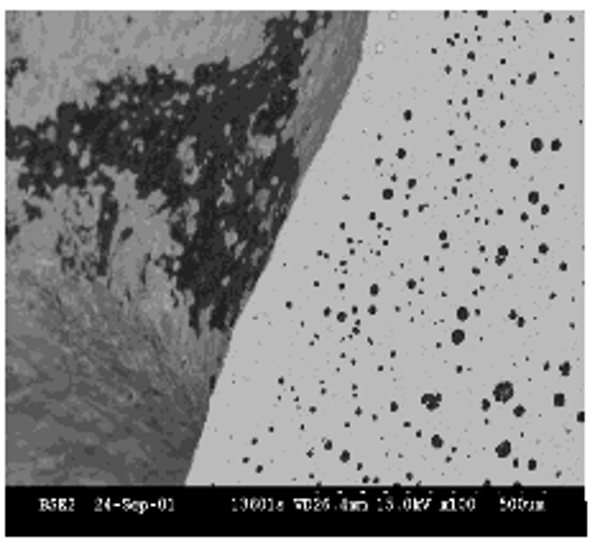
Nitrogen fissure defects
Predominantly a gray iron problem in medium to heavy sections adjacent to resin bonded mould or core materials, these are smooth-faced fissures or irregular cavities, perpendicular to the surface, extending a few millimetres into the casting. Internally, the cavities are black and shiny with dendrites penetrating into the cavity and a graphite depleted zone surrounding the holes. These defects are avoided by using low nitrogen core binder systems in conjunction with low nitrogen recarburizers such as ELGRAPH™ product, whilst any residual nitrogen can be neutralised by using ZIRCINOC™ inoculant which ties up nitrogen as relatively harmless zirconium nitride.
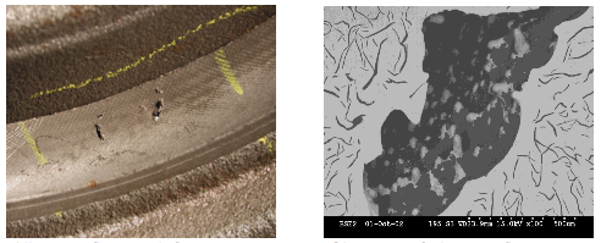
Elkem’s technical service engineers understand the mechanisms which can cause surface defects and we have the knowledge and the products to help you to avoid them.
ACCES MORE EXAMPLES OF TECHNICAL ADVICE
Contact us
Take your business to the next level by partnering with a world-leading material manufacturer.