What is a Silicone Resin?
Silicone resins are relatively low molecular weight polymers with a three-dimensional branched-chain structure. With excellent thermal stability their many properties make them suited for use as binders in paints, varnishes and impregnating products.
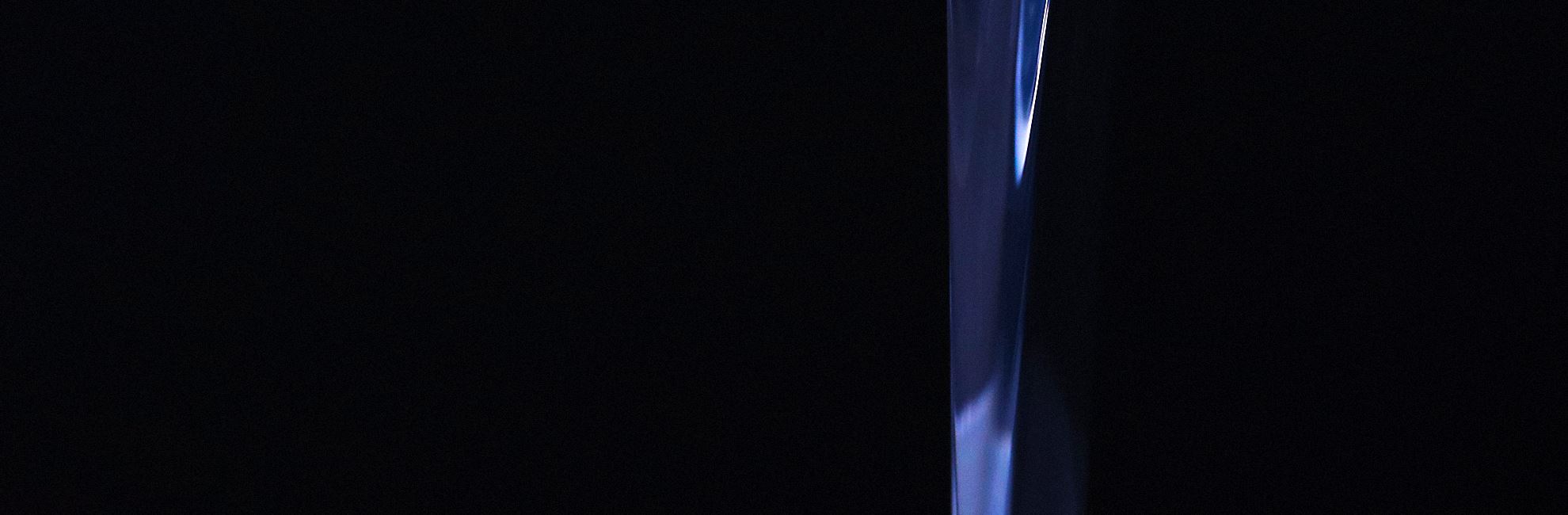
Chemical structure
Resins have very varied structures depending on the quantity of tri-functional T groups or sometimes quadri-functional Q groups that are introduced into the polymer during manufacture. Also on the type of non-reactive and reactive groups that are bonded to the silicon atoms.
Two of the most common types of non-reactive groups found in the siloxane chain also have a great influence on the resin's characteristics: methyl groups impart water repellency, release properties and surface hardness, whilst phenyl groups impart resistance to temperature and weathering, especially by UV-radiation, flexibility at high temperatures and compatibility with organic products. Two types of resins can be distinguished: methyl resins and methyl phenyl resins.
Three types of reactive groups allow the resin to crosslink.
-
Hydroxy groups are the most common type. They enable crosslinking to occur by a condensation reaction at room temperature either in the presence of a catalyst or in alkaline systems. The use of a catalyst and higher temperatures, especially in the case of methyl phenyl resins, generally accelerates the cure rate.
-
Alcoxy groups hydrolyse to give hydroxy groups at room temperature and in the presence of humidity. Curing then occurs as above. These resins are more stable when stored.
-
Vinyl groups react at moderate temperature by an addition reaction in the presence of platinum, as in RTV’s (Room Temperature Vulcanisation), or sometimes at high temperature in the presence of peroxides as in HCR’s (Heat-Cure Rubber).
Resins are generally available diluted in an aliphatic or aromatic solvents, emulsified into water, or diluted in silicone polymers to reduce their viscosity.
Silicone resin properties
After drying and crosslinking, resins form flexible or rigid, thermoset or thermoplastic films that confer remarkable properties to the treated surfaces. Their heat stability is outstanding: resins offer effective protection at constant temperatures of up to 250 °C and can withstand exposure to peak temperatures of up to 500 °C for short periods of time. They resist well to oxidation and have good dielectric properties, even at temperatures of up to 250 °C making them ideally suited for use in high-performance electrical insulation products. They also have excellent water-repellent characteristics and release properties.
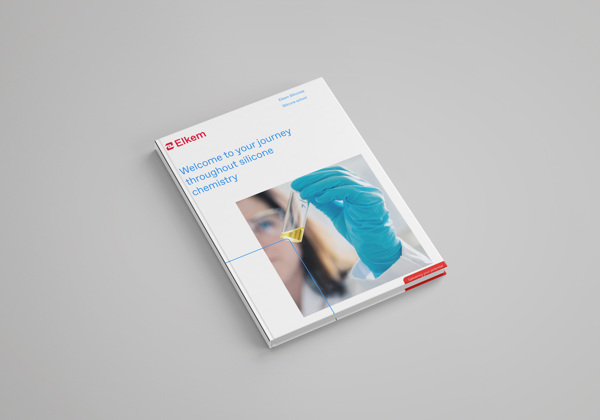
Revision sheet
Technology
Silicone Resin
Definition
​Silicone resins are made up of a chain of alternating silicon and oxygen atoms like oils, but in the form of a 3-D network. It can be liquid, powder or be dissolved into an aromatic solvent.
General information
​Silicone resin’s structure and physical properties vary a lot depending on its raw material type and process roadmap & condition. It depends on the requirements from terminal application.
Typical properties
Hydrophobicity, Hardness, Heat resistance, Chemical Resistance, Compatibility with organic compounds
Structural units
M= O1/2Si(CH3)3 D=O2/2Si(CH3)2 T=O3/2Si(CH3) Q=O4/2Si. Resin may be a combination of MQ, MDT, MDQ or / and further variants are created be the replacement of methyl by other functional groups such as Vinyl, Hydrogden, Phenyl, etc…
Processability
Usually, either sodium silicate or tetraethyl-orthosilicate (TEOS) are the primary raw material. Each process must go through 3 key steps “hydrolysis, silylation, end-capping” to a primary product, with a purification step as additional.
Application/final products
Resins are used in PSA (Pressure Sensitive Adhesives) as tackifier, in release coating as release force promoter, in sealing & bonding as adhesion promoter, in water repellent for building & textile
Silicone resins uses
Let’s see how resins are used in the industry. Most of the time silicone resins coming out of a silicone manufacturing facility will first be formulated. If we follow the path of our methyl silicones resins (MQ type), our customers use them to formulate into release agent products for many thermoplastic, thermo-setting or elastomeric substances like PU. The wide range of resins give formulators of release agents options and flexibility for their developments.
Those methyl silicone resins (MQ) offers many advantages:
- Odor free
- Very easy to use
- Excellent adherence to the surface of moulds
- High quality surface finish for the moulded article
- High thermal stability
- Reduces mould fouling
- Easy cleaning
Related applications
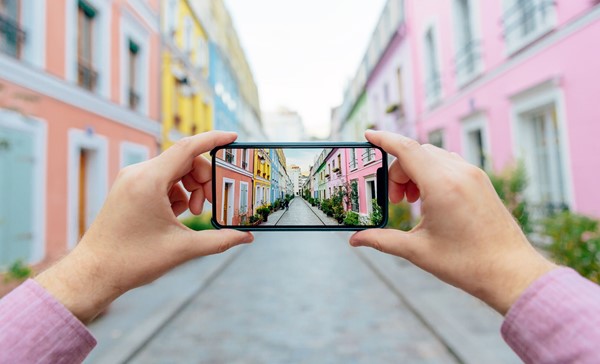
The paints industry is a major user of silicones resins as binders to improve the heat resistance of paints and renderings. They are also combined with organic resins to form polyester-silicone resin blends that are suited to continuous, pre-coating processes or so-called coil coating. Silicone resins are also used in electrical impregnating and insulation applications: they give effective protection against weathering and high temperatures. In industrial release and mould release applications, in which silicone oils are often used, the use of so-called MQ type resins prolongs the durability of the mould-release agent. Methylphenyl silicones are used to produce permanent, non-stick coatings that withstand high temperatures for kitchen applications. Special silicone resins are used in the water-repellent treatment of construction materials, of facades and in the consolidation of ancient monuments. In release coating of paper and films a very thin layer of "resin compound" is coated onto the substrate. In reality these complex compounds contain reactive oils, crosslinkers and a catalyst which cure to give the coating a resin-like structure.
Related products
Contact us
Take your business to the next level by partnering with a world-leading material manufacturer.