- Elkem
- Sustainability
- Policies, strategies and reporting
- Previous reports and related information
- Sustainability reporting 2018
- Elkem sustainability report 2018
Elkem sustainability report 2018
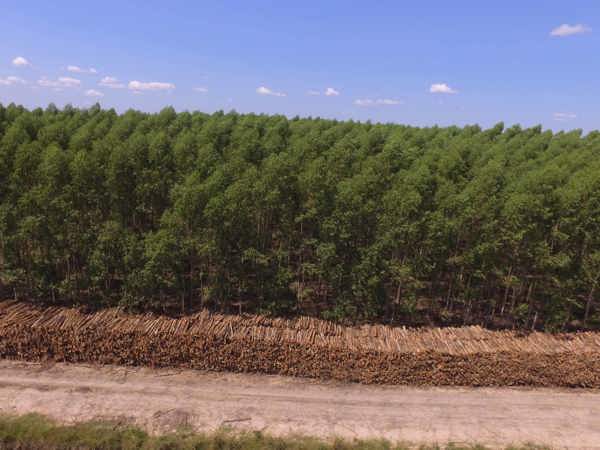
Introduction to Elkem and sustainability reporting
Who we are and what we do
Established in 1904, Elkem is one of the world’s leading companies in the environmentally responsible manufacture of metals and materials. Elkem is a fullyintegrated producer with operations throughout the silicon value chain from quartz to silicon and downstream silicone specialities as well as speciality ferrosilicon alloys and carbon materials. Elkem has more than 6,200 employees and consists of four business areas: Silicones, Silicon Materials, Foundry Products and Carbon.
Headquartered in Oslo, the company's 27 production sites and extensive network of
sales offices and agents around the world ensure proximity to customers and access to
attractive end markets.
On 22 March 2018 Elkem was re-listed on Oslo Børs.
Elkem’s total operating income in 2018 amounted to NOK 25,887 million, with an
EBITDA of NOK 5,793 million.
Please find more information about Elkem here.
Vision and values
Elkem’s vision is “to contribute to a sustainable future by providing advanced silicon, silicones and carbon solutions, adding value to our stakeholders globally”.
Our values are Respect, Involvement, Precision, Continuous improvement.
For full financial statements for 2018, please see the annual report, here.
Elkem’s sustainability work
Elkem’s mission is “to contribute to a sustainable future by providing advanced silicon, silicones and carbon solutions, adding value to our stakeholders globally”. For Elkem, sustainable growth means being part of the response to the great challenges facing the world.
Our products provide solutions to meet the demand driven by megatrends including increased energy needs, a growing population, rapid urbanisation and digitalisation. We believe sustainability is both a responsibility and a prerequisite to be at the forefront of our industry and to remain competitive in the future.
Elkem sees sustainability as a commitment, and our 6,200 employees in 28 countries are the ones who make it happen. The group is committed to harnessing technology and advancing the production of silicon, silicones and carbon materials to create new, innovative solutions and business models that promote a sustainable future. This has been the Elkem way of thinking since Sam Eyde established Elkem in 1904 and Carl Wilhelm Söderberg developed the Söderberg electrode in 1918. Their work came to define the future for Elkem and industry worldwide.
As corporate social responsibility includes a wide range of topics, we embarked last year on a process to identify which of these are most material to Elkem. This comes after a three-year process of restructuring and repositioning the company from a
traditional silicon and ferrosilicon producer to a vertically integrated supplier of silicones covering the whole value chain from quartz mining to a wide range of advanced silicon and silicone based speciality products. Elkem´s successful re-listing on Oslo Børs in March 2018 presented a good opportunity to engage more comprehensively with stakeholders on sustainability.
Stakeholder engagement
Stakeholder engagement
Cooperation and dialogue with stakeholders are essential for Elkem as we seek to be good neighbours and valuable community members wherever we operate around the world, be it small towns in Norway or major cities in China. Many of Elkem’s plants are cornerstone employers and of great importance to the local community with tax income, jobs, infrastructure and community development. As a long-term partner, Elkem values open dialogue with neighbours, local governments and other partners including research institutions, customers and suppliers.
Elkem's stakeholders:
- Shareholders, board of directors, owners
- Top management
- Customers
- Employees
- Local and national authorities
- Suppliers
- Local communities, family of employees
- Unions, union representatives
In 2018, Elkem has developed a stakeholder engagement tool to help us structure stakeholder engagement in the organisation and to enable a more thorough impact assessment. The tool pilot is now being tested and we plan to develop it further and implement it in key parts of the organisation in 2019. The aim is to get a better global overview of our stakeholder engagement.
Elkem’s annual internal stakeholder engagement survey shows how and where we interact with stakeholders. The participants in the survey were asked about typical stakeholder engagement types.
As cooperation and dialogue with stakeholders are essential to Elkem, the participants in our internal survey was asked to describe the overall relationship with their stakeholders. 80% answered that they had a trust-based relationship with their
stakeholders and 78% answered that it was a long-term relationship. Very few participants answered that the relationship to stakeholders is based on conflict (5%) and a poor understanding (3%).
Materiality Assessment
To ensure compliance with Global Reporting Initiative (GRI) and the new stakeholder landscape arising from Elkem´s re-listing on the stock exchange, the group carried out a more extensive engagement process with stakeholders last year. The materiality assessment table on the next page highlights Elkem´s priority issues on sustainability based on comprehensive dialogue with both internal and external stakeholders.
The material topics with highest priority in our materiality assesment can be found at the top right of the table. These topics are covered in our report.
Policies and reporting
Elkem’s management of Corporate Social Responsibility is defined in the following procedures:
- General policy of Elkem ASA
- Elkem policy for corporate social responsibility
- Mandate for the CSR steering committee
- Code of conduct
- Whistle blowing
- Anti-corruption policy
- Competition law compliance policy
The general policy for Elkem ASA is approved by the board and provides the overall strategic approach while the other procedures are approved by corporate management and give necessary details.
Elkem’s reporting of Corporate Social Responsibility is covered by the annual sustainability report that is prepared in accordance with the GRI Standards and in line with Oslo Børs’ guidance on the reporting of corporate responsibility.
Commitments
Elkem is committed to develop its business in support of the ambitions of the Paris climate agreement and the United Nations Sustainable Development Goals (SDGs). As a member of the United Nations Global Compact we ensure that our business is in line with the ten principles of the Global Compact. We are committed to following the United Nations Guiding Principles on Human Rights and Business, and have made available an updated statement for the UK Modern Slavery Act.
Elkem adheres to the principles of “the Norwegian Code of Practice for Corporate Governance” issued by the Norwegian Corporate Governance Policy Board (NCGB). The objective of the Code of Practice is that companies listed on regulated markets in Norway will practice corporate governance that provides division of roles between shareholders, the board of directors and executive management more comprehensively than is required by legislation.
Elkem’s silicones division is a member of the Responsible Care Global Charter which is the chemical industry’s global initiative to drive continuous improvement in environment, health, safety and security. This includes a commitment to managing chemicals safely throughout their life cycle. Elkem is committed to complying with international regulatory requirements and provides safety data sheets (SDS) for all applicable products in accordance with the UN Globally Harmonised System of Classification and Labelling of Chemicals (GHS) or its national implementations.
Elkem is an active member of national and European industry organisations such as Euroalliages, Eurometaux, the European chemical industry council (CEFIC) and industry associations in Norway and France.
Targets
We are committed to setting ambitious, but achievable targets for our material sustainability issues. This will allow stakeholders, from employees to investors, to monitor our progress in the years to come. The below targets reflect how we will overall manage engagement and reporting on sustainability. Each chapter in this report includes specific targets, which are aligned to our material sustainability topics and where introduced in the 2017 sustainability report.
Governance and compliance
Going further than the law
Governance and compliance is a prerequisite for value creation and trustworthiness. Elkem's strict ethical standards apply to all employees globally and we conduct training to enable our employees to make the right decisions and comply with our standards.
Elkem believes good corporate governance involves openness and trustful cooperation between all parties involved in the group: the shareholders, the board of directors and executive management, employees, customers, suppliers, public authorities and society in general.
In Elkem, we all are required to promote our values and business standards towards colleagues, business associates and society at large. Our governance documents set out principles for how business should be conducted. These apply to all Elkem entities. The board of directors approves the Elkem governance structure.
Our code of conduct is based on the principles of honesty and respect, and must be complied with regardless of where our operations are carried out. Corporate social responsibility forms an important part of Elkem’s business culture. Elkem is a signatory to UN Global Compact, and Elkem’s definition of corporate responsibility is based on the ten UN Global Compact principles concerning human rights, labour rights, environment and anti-corruption.
Compliance
Elkem is committed to full compliance with applicable rules and regulations wherever we operate around the world. Compliance is the responsibility of each business unit, but is also followed closely through the corporate system for internal boards and monthly business reviews as defined in the Elkem board of directors´ instructions.
Elkem’s board of directors endorses "The Norwegian Code of Practice for Corporate Governance" (the "Code") most recently revised 17 October 2018 and issued by the Norwegian Corporate Governance Policy Board (NCGB). The Code of Practice is available on http://www.nues.no/
All employees are given documented training on Elkem’s code of conduct and must sign the document to confirm their understanding and commitment to follow it. This includes training on Elkem policies related to business ethics, social responsibility and understanding how local culture and customs can influence the perception of what is acceptable in different situations. Training on Elkem’s anti-corruption and competition law compliance policies is also required for targeted groups. Sales, marketing and procurement resources also receive anti-corruption training. Elkem employees responsible for supplier audits receive additional training using recognised international audit standards and tools.
Elkem’s CEO is the formal owner of Elkem’s policy and programme for corporate social responsibility while governing documents are subject to board approval. The board of directors approves the sustainability report together with the annual report. The CSR steering committee is responsible for the sustainability report.
Each location and function are responsible for establishing a shared understanding of how Elkem’s CSR policy affects their specific working environment. They are also responsible for developing necessary procedures and routines to ensure full compliance.
Incidents in 2018
There were no identified material incidents of non-compliance with laws and regulations in 2018.
Anti-competitive behaviour
It is Elkem’s general policy to compete vigorously and fairly in full compliance with relevant laws and regulations applicable to its business. To ensure group-wide compliance, Elkem has adopted a competition law policy and manual that describes conduct that will or may infringe on competition law.
Absolute compliance with competition law is expected of all Elkem business units, its employees and representatives. Any failure to comply with competition law will be considered as a serious breach of the employee’s obligations towards Elkem. Elkem personnel considered as exposed to competition law issues are required to sign the competition law policy and manual and participate in competition law training facilitated by Elkem. Business unit leaders have the responsibility to take steps to implement Elkem’s policy in their respective organisations.
Incidents in 2018
No identified incidents of anti-competitive behaviour in 2018.
Environmental compliance
Environmental impact is one of Elkem´s key focus areas. Our EHS philosophy is to run operations with resource-efficient processes where negative environmental impacts are minimised throughout the value chain. Elkem is therefore committed to always stay within the rules and regulations governing environmental laws and regulations. Compliance is followed up by each plant as well as by the corporate EHS department and management through business reviews. All environmental deviations are documented, investigated and managed, even if they are within permit levels and legal restrictions, to learn from them and initiate actions to avoid them from happening again.
In 2018, there were no reported material deviations causing risk of environmental effects. There were however minor shortterm deviations from operating permits at some plants. These were quickly resolved and did not exceed annual limits or trigger
administrative sanctions or fines.
In 2018 our Chinese plants have been subject to close scrutiny from the Chinese environmental authorities as part of the general tightening of environmental regulations in China. Based on new regulations that were implemented abruptly some of our activities were temporarily closed down and ordered to invest in new abatement systems. This is being done in full compliance with requirements and all applicable activities have returned to operational status.
Incidents in 2018
No material deviation causing risk of environmental effect in 2018.
Anti-corruption
Elkem does not permit or tolerate any form of corruption. Elkem’s policy on anti-corruption applies group-wide and worldwide. Along with our EHS focus, anti-corruption is a top priority. The policy explains and elaborates on the content and implications of the anti-corruption policy for Elkem’s employees, representatives and partners. All Elkem personnel exposed to corruption risks must sign the anti-corruption policy and manual.
Elkem is present in several countries with high corruption-risk. Elkem also sells products to companies located in countries ranked in the bottom tier (i.e. very high levels of corruption) of the Transparency International’s Corruption Perception Index. Elkem conducts risk assessments on all operations group-wide and globally while the aforementioned high-risk countries receive particular scrutiny. All new suppliers of raw materials, goods and services are subject to pre-qualification based on corporate requirements within environment, health and safety, social responsibility, anti-corruption and compliance with laws and regulations. You can read more about our supplier requirements in the societal impact chapter, page 78. Examples of corruption risk includes the use of consultants regarding receiving public approvals, use of agents and joint ventures including local partners.
Risk assessments are typically conducted when entering into business arrangements in a new country where corruption is viewed as a major concern. Elkem will perform an integrity due diligence to assess the different risks related to corporate social responsibility, including corruption. The assessments may be done by relying on external specialists and will be regularly revisited. Elkem did not enter any new countries in 2018.
Elkem also undertakes a group-wide mapping of sales to companies located in countries with high corruption risk. The mapping ensures that the marketing departments have high-awareness to potential risks of unethical behaviour in these countries. This includes questions relate specifically to customer evaluation, CSR policy communication, documentation of sales, transaction transparency, and the application of Elkem’s standards when using agents and distributors.
All Elkem personnel exposed to corruption risks must sign the anti-corruption policy and document e-learning. This relates to the following personnel:
- Corporate management
- Division management teams
- Divisional finance managers
- Plant finance managers & controllers
- Treasury and credit management personnel
- Corporate business support personnel
- Technology management team / department leaders
- All project managers
- All managers in research and product development
- All sales and marketing personnel
- All procurement personnel
- Production managers
- General managers of subsidiaries
- Key managers in logistics/supply chain/raw materials
Each Elkem business unit is responsible for understanding the specific challenges regarding anti-corruption, the anti-corruption regulations applicable to its operations and for adopting adequate anti-corruption guidance and measures.
The target is that 100% of personnel in the target group should be trained within the first year of employment. For 2018 the target was met except for a few individuals that recently joined Elkem and have since been trained.
Elkem’s anti-corruption policy, as part of our CSR principles, is communicated and to a large extent forms part of the contracts with agents, distributors, partners, vendors and customers. They are also available on our website. All new suppliers must sign that they have understood and accept Elkem’s CSR principles.
Incidents in 2018:
There were no identified incidents of corruption in 2018.
Targets
Energy and environment
Zero-harm guides our work
Elkem strives to be an environmentally conscious company, with a safe and healthy working environment. Our environmental, health and safety (EHS) efforts are based on a zero-harm philosophy.
A zero-harm philosophy implies protecting the health and safety of all people working at all Elkem locations. It also means running operations with resource-efficient processes where negative environmental impacts are minimised throughout the value chain.
Using highly developed production technology, Elkem converts natural resources into products that today’s society is fullydependent on. With recent growth, Elkem is an integrated value chain covering all aspects of production from quartz to silicon and silicones. Each step of the process has its environmental challenges that we believe are managed in a sustainable manner. Our sustainability approach is based on the general principle of producing as efficiently as possible and with the maximum use of all input streams to avoid waste.
The process of converting quartz to silicon is a high temperature smelting process that consumes vast amounts of energy. As the main energy base for this production is hydropower at almost all of our smelters, the electrical energy supply does not have a climate effect. The process itself, however, uses carbon sources like fossil coal, charcoal and wood chips as a reductant in the chemical conversion. This gives emissions of CO₂, NOₓ and SO₂. These emissions are inherent to the process and cannot be fully removed with today’s technology. Our main strategy has therefor been to reduce our environmental footprint as much as feasible with today’s technology at the same time as we develop tomorrows technology that will be carbon neutral. Efforts include replacing fossil carbon with biocarbon by increasing the amount of charcoal and wood-chips in the process, rebuilding furnaces to reduce NOₓ generated in the smelting process and using more low-Sulphur raw materials to reduce SO₂ emissions. All of these have had a substantial positive effect on our environmental
footprint.
In 2018, Elkem presented a renewed environmental strategy for the board of directors confirming its commitment to:
- Full compliance with all applicable environmental regulations wherever Elkem operates worldwide.
- Create and sustain a strong environmental reputation wherever we operate worldwide.
- Ensure sustainable production and emissions/discharge control based on our knowledge of the environmental effects of our production. This also applies in countries where applicable environmental regulation is weak or non-existent.
- Strengthen our position in the development of technology and materials that enable reduction in greenhouse gas emissions throughout the world.
The strategy also provides KPIs, reported quarterly, for energy consumption, emission to air and water and waste/by-products.
Energy: consumption r
Energy is a critical input factor for Elkem’s production and represents a significant cost. Energy efficiency and sustainable use of energy is of upmost importance to secure necessary supply while at the same time reducing our global greenhouse gas footprint. New regulatory framework, such as concessions, directives, taxes and positive stimuli in the form of public support underscore the importance of focusing more strongly on energy efficiency.
Parts of Elkem’s value chain are highly energy intensive, with silicon, ferrosilicon and foundry alloys being produced in electric arc furnaces. Elkem’s smelting furnaces consume just under 5 TWh of electrical energy per year. The other processes in Elkem are considerably less energy intensive with the total of 1,4 TWh.
Elkem was an industrial pioneer in the utilisation of waste heat, with the first energy recovery system on a smelting furnace being installed already in the 1970s. Recovered heat from smelting furnaces can be utilised as hot water for district heating, steam for other production processes and to generate new electricity. Electricity is sold back to the grid while hot water and steam are used both internally and externally to supply other companies and communities in the vicinity of each plant.
Global records of total energy consumption have not been prioritised earlier as a very high percentage of the total is related to furnace production and has been well documented at a corporate level. With our renewed strategy and more detailed reporting systems this will be in place from 2019.
Total gross electricity consumption in Elkem globally in 2018 was 6,228 GWh, up from 5,279 GWh in 2017. This is because of the integration of the silicon plant Yongdeng, the silicones plant Xinghuo and the start of production at the ferrosilicon plant in Limpio, Paraguay.
Of the total gross power consumption of 6,228 GWh in 2018, more than 85% took place in countries or regions with close to 100% renewable power production. The increase in energy consumption is mostly related to new plants that now is a part of the Elkem organisation.
Globally, a total of 645 GWh heat and electricity was recovered from our plants, down from 689 GWh. This is due to lower capacity at our Chicoutimi plant. New electricity is generated at the Thamshavn and Bjølvefossen plants with a total of 209 GWh in 2018. Between 2016 and 2017 refurbishment and ramp-up of the energy recovery system at Bjølvefossen gave a substantial increase, while 2018 has been stable. By 2020, an additional 275 GWh of new electricity will come on line at the Salten plant as an approved strategic investment project started in 2018 is completed.
Elkem has not kept global records of energy consumption outside our industrial processes as this energy consumption comprises a small percentage of the total and is very time-consuming to collect. We will aim to improve our records of auxiliary power and fuels consumption over time.
For hot water to district heating there are numerous usages including heating of raw materials internally, supply to public building and sports arenas in local communities and sales to other companies with activities like land-based fish farming that need heat.
As a percentage of total electricity consumption, the amount of recovered electricity and heat went down from 13% in 2017 to about 10% in 2018 due to the integration of new plants that does not have energy recovery facilities.
1)2016 numbers do not include Elkem Rana, Xinghuo and Yongdeng. 2017 numbers do not include Elkem Yongdeng.
Consumption of reduction material
Elkem’s electric arc furnaces use both fossil and biogenic carbon as chemical reduction materials in the metallurgical process. Total use of fossil reduction materials in Elkem globally was 726,267 in 2018, up from 695,004 in 2017.
Consumption will vary from year to year based on market conditions and capacity utilisation. The increase is mainly due to the integration of Yongdeng Silicon Materials in 2018.
Total renewable reduction material consumption in Elkem globally was 364,424 tonnes in 2018, a 4% increase from 2017.
Waste management
With the expansion of Elkem to include the chemical production of silicones from silicon, the characteristics of our waste streams have changed. From our traditional smelting activities waste consisted mainly of non-hazardous inorganic materials such as slag, product fines, quartz fines and a smaller quantity of organic fines from wood-chips and charcoal. For all of these, extensive projects have been initiated to re-cycle and re-use instead of depositing in landfills. Many of these have been very successful by both creating new products and by better utilisation of raw materials.
With silicones there is much higher content of organic waste and hazardous waste from the different production processes. Hazardous waste is mainly managed by certified external suppliers, while other waste will either be incinerated or landfilled. Many projects have also been initiated here to reduce waste at its source and to regenerate chemicals for re-use instead of destroying or depositing them.
Several plants have a zero waste to deposit target and have accomplished significant reductions over the last years. Waste to landfill in 2018 was 195,000 tonnes. About 1,300 tonnes of this was hazardous waste and has been managed in accordance with local public regulations. There were no significant spills, defined as spills that have a lasting environmental impact, in 2018.
However, there have been incidents related to loss of containment in tank facilities, but without substantial environmental impact.
Emissions
With today’s technology, the production of metals and materials on an industrial scale is not possible without the emission of various substances that can be harmful if not controlled. These include CO₂, NOₓ, SO₂, PAH and dust. As some of these are inherent to our production process, emission levels vary with production volume from year to year. Elkem works continuously to reduce these emissions and has dedicated R&D activities working with all major emissions.
CO₂ emissions and trading schemes
More than 75% of the total CO₂-emissions from our production come from the smelting process. As this cannot be measured directly, emissions are calculated based on third party certificates of carbon content (TC) in raw materials (coke and coal). Numbers for CO₂ from other sources, including heating and fuel, are
based on standard conversion factors in accordance with EU/ ETS Guidelines.
Most of our smelters are subjects to the EU/ETS system and its external revision schemes. From the start in 2013 Elkem was granted on average 1.2 million free allowances per year as part of the EU system to avoid carbon leakage where production would be moved out of Europe to other countries without carbon trading schemes. When it was identified that smelters in Norway had been allocated fewer free quotas than other countries in Europe, the allocation was appealed. At the end of 2018 a decision was announced increasing the number of free quotas at two of Elkem’s Norwegian smelters.
The total emission of CO₂ from our processes was 2.54 million tonnes in 2018. This will vary year on year based on market conditions and capacity utilisation. The last years we have seen an increase in our total CO₂ emissions. All of this can be related
directly to production expansion. In 2017 Elkem acquired an existing production facility with 2 furnaces in Mo I Rana Norway and in 2018 another with 4 furnaces in China. All of these were existing production facilities and do not increase Norway’s or China’s total CO₂ emissions. In addition, Elkem started 1 smelting furnace in Paraguay giving a national increase in CO₂ emissions in Paraguay. This furnace is however run on hydroelectric power and uses only bio-carbon as a reductant making its operation close to carbon neutral.
As far as net CO₂ emissions are concerned, this is dependent on improved production yield and increasing the amount of reduction materials from non-fossil sources that can be used. Our goal is to reduce our fossil carbon footprint in our Norwegian smelters with 20% by 2021, and with 40% by 2030. We are working with partners to develop efficient and more environmentally friendly production of charcoal to silicon and ferrosilicon production.
CO₂
In 2018, Elkem emitted 2.54 million tonnes of fossil CO₂, a 30% increase from 2017. This increase is mainly due to the expansion of plants in our organisation.
About 75% of the total CO₂ emissions were generated in the reduction processes in the smelters where carbon (C) reacts with oxygen in quartz to obtain silicon/ferrosilicon.
Our goal is to replace fossil emissions with biocarbon by 20% in our Norwegian smelters by 2021. The biogenic emissions in 2018 was 313,500 tonnes, equal to 20,7% of our CO₂ emissions. The emission of biogenic CO₂ origniates from woodchips and charcoal used as alternative raw material in the silicon and ferrosilicon smelters.
Other emissions
Elkem has significant emissions of NOₓ, SO₂, and dust. Emissions vary mainly due to production volume.
NOX
Elkem's NOₓ emissions saw a small decline from 7,110 tonnes in 2017 to 7,070 tonnes in 2018, including new plants in the calculation. This reduction comes as a result of several initiatives and projects at our plants, mainly supported by the Norwegian NOₓ fund. For our Norwegian smelters, Elkem has seen a 5% decrease
in our NOₓ emission, from 5774 tonnes in 2017 to 5462 tonnes in 2018.
SO₂
In 2018, Elkem emitted 9,000 tonnes, up from 7,900 tonnes. For SO₂ the main focus has traditionally been on sourcing raw materials with a lower sulphur content. As this potential is limited, scrubbing systems are also being considered where this is feasible. In 2018, Elkem Carbon (Norway) finished the installation of a large SO₂ filter with support from the Norwegian SO₂ fund. Unfortunately, the installation has not operated as expected due to technical issues and has therefore been out of operation for most of 2018. These technical issues will be resolved early in 2019. Elkem Bjølvefossen is also evaluating a similar project.
Dust
Elkem allocates significant resources to combat dust. However, extremely high temperatures and ultrafine particles that disperse very quickly make it especially difficult to capture dust generated in some of the production processes.
For 2018, Elkem emitted 1.8 million tonnes of dust (PM/particular matter). This was a decrease from 2 million tonnes in 2017. The 10% decrease is highly welcome and comes as a result of continous improvements. Our overall goal is a 30% reduction by 2025, based on 2015 numbers. We are pleased to see that we are on the way to reach that target.
Targets
Attractive employer
Striving to be an even better workplace
Elkem´s skilled and dedicated employees are the basis of our success and Elkem must strive to remain an attractive employer, both to retain and to attract new employees. Important areas of action are health and safety, training and competence building as well as promoting equality and diversity.
Elkem´s skilled and dedicated employees are the basis of our success and Elkem must strive to remain an attractive employer, both to retain current employees and to attract new employees. Important focus areas for this are health and safety, training, competence building and the promotion of equality and diversity.
Environment, health and safety (EHS) are part of the foundation of the company and are always our first priority. Our EHS efforts are based on a zero-harm philosophy. The safety of our employees is paramount. We strongly believe and have shown at many plants that our production can be done without any harm to our people.
Supported by a strong company culture, we work continuously to be a safe and attractive employer, for current and future employees. Organisational development, continuous talent management and systematic competence development are key
to the successful growth of the company, especially now that we are growing as a company.
Elkem has more than 6,200 colleagues after the acquisition of two plants in China, Yongdeng Silicon Materials in Lanzhou and Xinghuo Silicones in Jiangxi, this equals 35% more employees in the company.
The number of contract employees in Elkem was 833 in 2018. Contractors deliver services of many kinds at Elkem’s plants and other locations around the world and are subject to the same EHS requirements as our own employees. Contractors receive training and follow-up to ensure that they have a safe and healthy working environment. Total number of contractors by region in 2018 was 633 in Asia, 146 in Europe, 0 in Africa and 54 in the Americas.
Common culture: Elkem Business System
As in all organisations, Elkem evolves and develops over time and the company culture evolves with it. Elkem’s values are involvement, respect, precision and continuous improvement. Together with the Elkem Business System (EBS) they are at the core of Elkem’s company culture. EBS is our business philosophy and a toolbox that gives a common language and working methods for all employees to achieve both personal and business success. EBS covers all areas of work, including productivity, quality and cost efficiency. The EBS method and philosophy applies throughout the organisation, and training of our staff is highly prioritised.
Occupational health and safety
Elkem does not accept that injuries or illnesses are unavoidable facts in our industry. Full understanding of health and safety risks and challenges have high priority at all plants. Elkem's statistics clearly show that it is possible to run difficult and potentially dangerous operations with a large work force without injuries. Several of our plants have achieved this for a number of years in succession. The status of Elkem’s safety work is discussed every week at division and group management level.
However, Elkem’s production processes also have a number of health challenges that are managed daily in Elkem’s organisation. The main exposures that may lead to occupational diseases are:
- Exposure to quartz dust in mining, transportation and storage of quartz, and exposure to SiO2 dust in smelting halls that may cause lung diseases.
- Exposure to PAH components in carbon paste production that may cause cancer.
- Exposure to toxic chemicals in chemical processes to produce siloxane and silicone products.
- Exposure to noise.
- Exposure to ergonomic challenges that may give long-term musculoskeletal damage.
All of these exposures are carefully managed at each applicable site with containment, work and work station adjustment, and, when necessary, personal protection equipment that is provided free of charge to all employees. Many initiatives have also been implemented through the years to reduce exposure by reducing/ eliminating sources of dust and noise, and substitution of hazardous substances in the production process.
Employees who are exposed for hazardous dust, chemicals and noise are also subject to extended medical follow-up. A medical examination sets a baseline for their health condition when hired, and routine medical examinations follow-up that this does not change over time.
Injury severity
Elkem measures injury severity based on the short and long-term effect the injury has on the injured person’s health and capabilities. We use OSHA’s definition of recordable injuries for reporting and define Lost Workday injuries as H1, and Medical Treatment / Restricted Work injuries as H2.
In 2018 we reached the second best total recordable injury rate (H1+H2) in Elkem’s history with 2.2 injuries per million working hours, down from 3.1 in 2017. Our best result was in 2015 with 1.8. Part of this positive development is due to our growth with a high increase in the number of working hours, but we also see a very good improvement in the number of recordable injuries for own employees. Sadly, we saw an increase from 13 injuries (2017) to 20 injuries for our contractors. This again shows that we can never loose focus on our zero-harm philosophy and goal.
In Elkem, injury severity is tracked as low, medium and high severity. Low severity injuries give no permanent damage and have a short recovery time, medium severity injuries may have a longer recovery period, but no substantial permanent damage, while high severity injuries give substantial permanent damage or worst case, causes death.
Although Elkem's total recordable injury rate numbers were record low in 2018, Elkem did have an increase in severity. In 2017 we had three injuries with high severity, while the number increased to eight in 2018. 83.4% of all recordable injuries (both own employees and contractors) were registered as low and medium severity in 2018. This is down from 95.3% in 2017, because of the increase in severe injuries.
Elkem had no fatalities in 2018.
Absentee rate
Absenteeism is the key performance indicator for health in Elkem. The average rate of absenteeism measured in percent of available working days for 2018 was 2.5%, down from 3.5% in 2017. The absentee rate has been on a downwards trend since 2011, and this year’s number is the best in nine years. This is partially an effect of growth in areas where the threshold for taking sick leave is higher than in Europe, but also indicates a strong work environment in the organisation. A small percentage of the total sick leave is work related. Ongoing activities to increase health and wellbeing at Elkem locations include working environment assessments and improvement efforts in the areas of ergonomics, chemical control and noise and dust reduction.
Occupational disease rate
For the past three years there has been very few reports of possible occupational illnesses. Most of these are low-key ergonomic issues concerning strain and pain. There have also been several reports of possible lung disease in connection with dust exposure, but none have been fully documented as work related. All of these have been in Europe.
Diversity and equality
Elkem is committed to equal opportunities for all our employees in an inclusive work culture. We appreciate and recognise that every individual is unique and valuable, and should be respected for his or her individual abilities. We do not accept any form of harassment or discrimination based on gender, religion, race, national or ethnic origin, cultural background, social group, disability, sexual orientation, marital status, age or political opinion.
Elkem is an international company with a presence on four continents. Having employees to match this global presence, with diverse cultural and individual backgrounds, is necessary for the company to succeed. Elkem is a local employer and aims to employ local management and staff wherever we are present.
Following up the principle of non-discrimination is the responsibility of each unit manager. Elkem has an internal notification service (whistle-blowing) that employees can use to note their concerns about possible breaches of Elkem’s ethical guidelines or other possible unethical or illegal actions. This can be used to alert management of instances of discrimination.
The #metoo campaign on sexual discrimination raised awareness and discussion on several Elkem locations through 2017 and 2018. A pilot project about diversity and inclusion has been developed in 2018, and the first workshops will be held early 2019. The focus of the workshop will be different kinds of discrimination and possible ethical dilemmas in our work day. The pilot will be evaluated and considered for the organisation as a whole.
Incidents in 2018
There was one case of verbal sexual harassment reported to corporate level in 2017. The case was handled according to Elkem’s corporate procedures. The same case continued in 2018 and resulted in termination of employment.
Female share
The process industry is generally male-dominated. Women are, however, increasingly expressing an interest in working in our industry as increased automation leads to less heavy manual work and a high focus on environment, health and safety gives a better working environment and more sustainable operations. Elkem values gender diversity and aims to achieve a better gender balance year on year.
The percentage of female employees in Elkem has remained stable and low at 22% the last years. We experienced an increase in female share of the company to 25% in 2018, due to the integration of the Chinese plants of Elkem Xinghuo Silicones and Elkem Yongdeng Silicon Materials. Asia is the region with the highest number of female employees, with 29%.
Since the two new plants Xinghuo Silicones and Yongdeng Silicon Materials account for a 35% increase of employees in the organisation, any change is naturally affected. A positive change with this integration is the substantial increase in female blue-collar
employment from 7% to 18% in 2018.
However, Elkem saw a drop in the share of female leaders. One concrete action to improve our share of female leaders is to actively encourage women to apply for management positions internally. At least 50% of participants invited to Elkem’s leadership training programmes are women. The female participation
rate in the programme in 2018 was only at 25%.
Elkem does not have the share in age groups at group level available for 2018.
Board of directors and management
Elkem’s board of directors has eight members from Germany, France, China and Norway.
The female share of the board is 50%. One of the eight board members is in the age group 30–50 years old. The rest of the members are 51 years or older. None of the board members are from minority groups.
The corporate management team of Elkem consists of 10 people. Only one of the 10 is a woman. Two of the members are in the age group of 30 to 50 years old, the rest are 51 years or older. In 2018 Elkem started mapping the female share of leaders
and boards in our divisions to get a better overview and start tracking. The mapping shows great differences within the organisation. Some places in the organisation women account for 50% of internal boards and plant management, other locations there are no women in the boards or management at all.
Development and training
Elkem is active in a large number of demanding markets and the need for continuous developments and improvement is constant. The organisation’s improvement work needs to be targeted, fastpaced and of high quality. Elkem actively uses employees’ dayto-day work situation as the primary arena for learning. We believe that the best way to develop new skills is to participate in actual improvement processes and problem solving based on the EBS principles. We also consider taking on new responsibilities as a very important way of learning and developing. To strengthen our learning-by-doing approach we also offer a number of in-house training programmes. Training within various skills is part of the individual development plans for employees.
Elkem’s global target is that 100% of employees of all positions and locations shall have an annual development discussion with their leader. In 2018, 59% of employees had such discussions. On that note, 83% of all Elkem units achieved 90% or higher implementation rate. Without Yongdeng Silicon Materials and Xinghuo Silicones, the number of employees that received development discussions was 91%, one of the best numbers we have seen in the company. 74% of our location met our 100% target in 2018. In 2019, we will increase the efforts especially at our two new plants,
and strive towards our goal of 100% in the whole organisation.
Turnover
Turnover rate is an indication of attractiveness and how well Elkem manages to retain our employees. The turnover rate is the so called unwanted leavers, the number of people that left Elkem that does not included retirement and similar. Total turnover rate in the Elkem group was 5.4%, down from 6% in 2017.
The female share of new hires was over all 22.5% and the female share of leavers was 22.8%. The numbers are not available by age at group level.
Collective bargaining agreements
Elkem complies with local statutory requirements regarding freedom of association in all countries where we are present. Pursuant to the provisions of the Norwegian Companies Act, employees have two representatives and two observers on the board of Elkem ASA.
The level of organisation varies from country to country. In some countries the operators are organised under one collective bargaining agreement. In other countries there are no unions represented in Elkem’s entities. Elkem supports the right to exercise freedom of association and collective bargaining and in general has good cooperation with the unions. This also includes our suppliers’ employees, were information about this is found in contractual agreements. Information about the number of employees covered collectively by bargaining agreements is currently not available.
Child and forced labour
Elkem has operations in several countries where there is a risk of child labour and forced labour, notably India, Malaysia and Paraguay.
Working at some supplier production sites or some of our own plants is considered high risk work and must only be done by trained and qualified people.
The age limit for working in Elkem is 18 years of age, with the exception of some vacation substitutes and vocational students who can be 16. They are only allowed to do light and simple work that is deemed safe and does not conflict with school participation.
Elkem’s suppliers have contractual obligations to ensure that no children under the age of 15 (14 in some selected countries) work at our supplier’s plants and that they limit hazardous work and night work to persons over 18 years of age. Elkem adheres to the UN Guiding Principles on Human Rights and Business.
Incidents in 2018:
There were no reports of child or forced labour in Elkem or with our suppliers in 2018.
Targets
Sustainable footprint with great reach
Elkem’s operations have significant impact on society throughout the value chain. In addition to own operations, Elkem also has a significant footprint through its procurement of raw materials, capital goods and services. We set high standards for ethical conduct and social responsibility in our supply chain and monitor it closely.
This impact has both positive and negative sides. On the positive side, our operations create stable employment and tax revenue in addition to developing and producing products and materials that are essential to our way of life and to the changes that are necessary as we see the effects of climate change. On the negative side there is high energy usage and harmful emissions that must be closely monitored and effectively mitigated.
The process industry plays a major role in the transition to a low carbon society. In addition to reducing own emissions and increasing energy efficiency, Elkem contributes to the green transformation by delivering materials, technology and solutions that are necessary for the transformation in other businesses and sectors around the world. Solar panels, wind mills, electric vehicles, low emission transportation and infrastructure, smart phones, batteries and cables are all dependant on products and materials produced by companies like Elkem.
Global megatrends affects our business stratgy and drive growth for Elkem’s products and solutions. This requires that we specialise. Elkem's products serve demand driven by six megatrends that are strategically important to Elkem: Sustainability, energy demand, rapid urbanisation, increased standard of living, ageing and growing population, and digitalisation. In the illustration on the page to the left you can see how the different global trends are linked to our process, products and solutions, and how we contribute to the UN Sustainable Development Goals. Elkem believes sustainability is both a responsibility and a prerequisite to be at the forefront of our industry and to remain competitive in the future.
Supply chain and raw materials
Elkem sources raw materials, capital goods and services for our operations around the world. Elkem sets high ethical, environmental and social standards that companies must meet to become our suppliers.
Elkem’s corporate supply chain function holds the overall global responsibility for outlining and maintaining Elkem’s procurement and logistics strategies and policies. Elkem’s main purchasing categories are raw materials, equipment and construction and maintenance services on site. The function is working internationally across all divisions in the company, and the focus is to improve Elkem’s total procurement and logistics cost in a sustainable way.
Elkem’s total procurement spend in 2018 was approximately NOK 15 billion, covering supplies of raw materials, materials, energy, goods, services and logistics. The active supply base consists of about 15,000 suppliers globally – of which almost 70% in Europe.
Supplier requirements
All new suppliers of raw materials, goods and services are subject to pre-qualification based on corporate requirements within environment, health and safety, social responsibility, anti-corruption and compliance with laws and regulations. Risk assessments are done before suppliers are approved. Risk-exposed suppliers are subject to detailed requirements from Elkem. Elkem also requires that suppliers and their sub-contractors follow Elkem’s principles. Elkem is implementing improved database and contract management systems to ensure compliance and governance
in these areas.
Elkem has developed detailed requirements for high risk suppliers and contractors regarding health, safety and environmental standards for operations like mining, transportation, storage and loading, and is actively involved in the promotion and monitoring of safe and decent working conditions. This includes health and safety training and providing correct personal protection equipment for suppliers’ employees when necessary. Age control to prevent child labour and ensure responsible working conditions for young employees is also carried out. Elkem requires suppliers and contractors to engage their employees with written contracts on fair terms, and to give them information about their right to organise and collectively bargain with management where this is legally possible.
Elkem’s requirements are regularly discussed in meetings with suppliers. High-risk suppliers must document their understanding of legal requirements and hazards in their operations and present plans showing how risk will be eliminated or controlled while working for Elkem. Elkem performs audits and inspections, both in connection with routine visits for quality, technical and business follow-up, and as unannounced site visits. External auditors also conduct supplier audits on Elkem’s behalf.
Violations of Elkem’s requirements are registered and addressed with verbal or written warnings in addition to requests for improvements when necessary. Repeated violations may lead to requirements for speedy implementation of improvement plans, financial penalties, or termination of contracts with immediate effect.
Supplier screening
New suppliers of raw materials and hardware and services to plants and investment projects are screened using social and environmental criteria. The goal for 2019 is to continue improving documentation of screening and follow-up and to implement a global supply chain risk management system.
Supplier audits
For raw materials the number of suppliers is relatively low, and a structured auditing programme is in place to ensure that all existing suppliers receive regular audits. For suppliers of goods and services such as hardware, plant equipment and services the number of suppliers is high. New suppliers are assessed for social and environmental criteria, and regular audits are performed by plant personnel or corporate personnel. In 2018, Elkem entered into a partnership with a global supply chain risk management solution that will support contractual relationships with existing and new suppliers in keeping their information up-to-date in a web portal, ensuring widespread visibility to their current qualification status and competencies. The system will also be used to keep a central record of supplier audits.
Local communities
Input from local communities is valuable information that helps us improve. Important topics for dialogue with local communities are community development projects, job security, safe operations, emissions and other environmental issues, and traffic generated by the plant. Complaints raised by local communities, and traffic incidents related to our operations are registered and managed in accordance with good practices for incident and deviation management.
Dialogue with local communities is the responsibility of each plant or site manager and is carried out both formally and on an informal day-to-day basis. A number of Elkem plants have local initiatives and support programmes for better education, sports activities, better local infrastructure, local community poverty reduction/food support or other social impact initiatives. There are clear guidelines for what is permitted to avoid corruption.
Being part of local and regional formal networks are also an important way of understanding the needs of local and regional communities. Several of Elkem’s plants are members of business organisations, research and development clusters or other networks. In our stakeholder survey 65% of the participants said their unit were part of some sort of local/regional network.
Stakeholder
Key issues for the stakeholders
Employees
Safe jobs, high EHS standard, sustainable work situation, development/career opportunities, contribute to EHS and business improvements, salaries, benefits and compensation (employee welfare), equal opportunities, sustainability (CSR).
Authorities
Environmental regulations, industrial practice and trust, good environmental performance, open communication, compliant with laws – labour and environment, community development, pay taxes, active participator in dialogue, coordination with fire and police force.
Management
EHS results, financial results, strategic direction, ethical business, CSR issues, compliance, all to follow Code of Conduct, sustainable business, leadership development, full compliance with laws.
Customers
High quality of product, highly trustworthy partner, good coordination in supply chain, technical improvements, fair/reasonable pricing, ethical and responsible behaviour, timely delivery of product, product innovation.
Suppliers
Ethical and responsible behaviour, value addition, anti-corruption work, anti-bribery work, highly trustworthy partner, transportation.
Local communities
Community support/development, EHS, sustainable business, employment prospects, reliable employer, visible in the community, open and trustworthy dialogue, environmental performance and perception.
Unions
Respect of agreements, good work climate, good dialogue, constructive partnership.
Shareholders
Profit, strategic direction, EHS results.
Contact us
Take your business to the next level by partnering with a world-leading material manufacturer.